پوششهای PVD بر روی قطعات صنعتی و تزئینی در رنگ های متنوع با ساختار مختلف برای کاربردهای گوناگون تولید می شود.
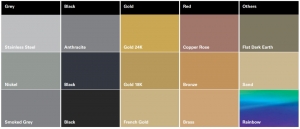
شکل۱-رنگهای استاندارد تولید شده با استفاده از PVD
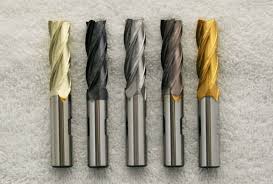
شکل۲- تولید مته های با پوشش PVD
نسل اول: اولین پوشش ایجاد شده با روش PVD پوشش های سخت نیتریدی عناصر واسطه مانند TiN ، CrN و ZrN بوده اند. سختی بالای این پوشش ها در مقایسه با فولادهای تندبر و کاربید سمانته قابل توجه بود. همچنین به خاطر ظاهر جذابشان برای صنعت دکوراتیو و تزئینی نیز مورد توجه قرار گرفتند. پایداری حرارتی این پوشش ها برای کاربردهای ماشینکاری در سرعت بالا مناسب نمی باشد. به طوری که پوششهای TiN در دمای 450 درجه سانتی گراد اکسید و تجزیه شده و از بین خواهد رفت.
نسل دوم: پایداری حرارتی پوشش های تک فازی از جمله TiN با افزودن عنصر آلیاژی از جمله Cr، Al، و Y به داخل ساختار TiN بدست می آید. به عنوان مثال پوشش های نانوساختار TiAlN که به عنوان جایگزین TiN و پوشش مقاوم به اکسیداسیون مطرح است. با وجود سختی بالا، به دلیل تشکیل محلول جامد، مقاومت به اکسیداسیون بسیار خوبی را از خود نشان می دهد. در این پوشش با تشکیل لایه نازک نانومتری Al2O3 در دمای بالا موجب حفاظت پوشش در برابر ادامه اکسیداسیون خواهد شد.
نسل سوم: بهبود خواص مکانیکی با ایجاد پوشش های چندلایه های و ابرشبکه حاصل می شود. واژه «ابرشبکه» به پوشش های چندلایه گفته می شود که تناوب لایه ها با ضخامت کمتر از ۱۰ نانومتر باشد. یکی از اولین مثال های پوشش های ابرشبکه، TiN/VN و پوشش TiN/NbN می باشد. با انتخاب ترکیب مناسب برای پوشش های چندلایه، امکان بهبود خواص پوششها از قبیل مقاومت در برابر سایش، خوردگی و اکسیداسیون و افزایش چکشخواری وجود دارد.
نسل چهارم: پوششهای نانوکامپوزیتی شامل حداقل دو فاز است: یک فاز نانوبلوری و یک فاز آمورف و یا دو فاز نانوبلوری مانند TiAlSiNs. ترکیب دانه های نانوبلوری سخت (مانند کاربیدها و نیتریدها) و مواد آمورف(مانند DLC) با مدول الاستیک بالا، موجب دستیابی به سختی بالا و بازیابی الاستیک خوب شده است. پوشش های نانوکامپوزیتی نوعاً به عنوان پوششهای فوق سخت شناخته می شوند که مقدار سختی آن ها بیشتر از۴۰GPa است.
نسل پنجم: تلاشهای اخیر بر توسعه پوششهای سخت، مقاوم به سایش و ضریب اصطکاک پایین متمرکز شده است. برای این مهم می توان از موادی چون گرافیت، MoS2 و مواد اکسیدی در پوشش نانوکامپوزیت استفاده کرد. پوششهای مقاوم به سایش و خود روانکار با استفاده از فازهای روان کننده مانند گرافیت، کربن آمورف و MoS2 در داخل پوشش توسعه یافته است. ضریب اصطکاک پوششهای خود روانکار در این حالت بین ۰.۱ تا ۰.۰۱ خواهد بود. تحقیقات نشان می دهد خواص سایشی پوششهای کلاسیک با استفاده از لایه نازک DLC (شبه الماس) به عنوان لایه خارجی بهبود یافته است.
قطعات صنعتی |
پوشش | |||||
TiN | TiC | CrN | AlTiN | ZrN | DLC | |
میکرو سختی(HV) | ۲۰۰۰-۲۵۰۰ | ۲۷۰۰-۳۰۰۰ | ۲۱۰۰-۲۵۰۰ | ۳۰۰۰-۳۷۰۰ | ۲۲۰۰-۲۶۰۰ | ۱۵۰۰ |
ضریب اصطکاک در حالت خشک(µ) | ۰.۵ | ۰.۴ | ۰.۵ | ۰.۴ | ۰.۵ | ۰.۱ |
ضخامت پوشش(µm) | ۱-۴ | ۱-۴ | ۱-۴ | ۱-۴ | ۱-۴ | ۱-۴ |
دمای اکسیداسیون(֯C° ) | ۵۰۰ | ۴۰۰ | ۶۵۰ | ۹۰۰ | ۵۵۰ | ۴۰۰ |
رنگ ظاهری | طلایی | خاکستری | نقره ای | بنفش تیره- رزگلد | طلایی روشن | نوک مدادی |
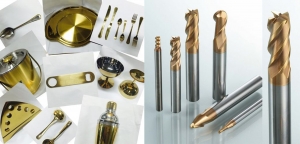
شکل۳- پوششTiN ایجاد شده بر روی ابزار و قطعات دکوراتیو
پوشش TiN: نیترید تیتانیم اقتصادی ترین لایه پوششی است که همواره به دلیل رنگ طلایی جذاب مورد تقاضای مشتریان بوده است. این پوشش اولین بار با روش PVD تولید شد. از این پوشش برای رنج وسیعی از کاربردهایی که نیاز به افزایش سختی، مقاومت گرمایی، مقاومت به اکسیداسیون و روانسازی دارند مورد استفاده قرار می گیرد. همچنین دوستدار محیط زیست بوده و در صنایع دارویی و پزشکی مورد استفاده قرار می گیرد. در صنایع ابزارسازی نیز کاربرد وسیعی برای بالابردن عمر و مقاومت به سایش ابزارهای برش، سوراخکاری و… دارد. در حوزه دکوراتیو نیز کاربرد بسیاری برای پوشش شیرآلات، زیورآلات، بلور و کریستال، قاشق و چنگال استیل، سرامیک و … دارد.
منبع: مهندسی نانو پوششهای سخت و مقاوم؛ دکتر حسن علم خواه