پوشش دهی با استفاده از رسوب فیزیکی بخار (PVD) به دو روش کلی تقسیم میشود:
۱- تبخیر حرارتی (Evaporation)
۲- کندوپاش(Sputtering)
که هر کدام از آن ها با چند مدل مختلف انجام می شوند که در ادامه توضیح داده خواهد شد.
۱-۱- تبخیر حرارتی Thermal Evaporation:
فرآیند تبخیری با بهره گیری از فیلامان تنگستنی، برای ذوب فلزاتی مانند آلومینیم و مس که نقطه ذوب کمتر از ۱۵۰۰ درجه سانتیگراد دارند مورد استفاده قرار می گیرد. بعد از رسیدن فشار محفظه به محدوده ۵-۱۰ تور، از طریق الکترود مسی (دارای آبگرد)، جریان بالایی (در حدود ۱۰۰ تا ۲۰۰ آمپر) به بوته تنگستنی اعمال شده و موجب تبخیر مواد هدف (تارگت) که در داخل بوته قرار گرفته می شود. از عواملی که سبب کنترل سرعت رسوبگذاری در این روش خواهند شد، دمای ذوب ماده هدف، مقدار جریان اعمالی و فشار محفظه است.
مزایا:
۱- تجهیزات ارزان قیمت نسبت به کندوپاش
۲- مواد هدف (تارگت) ارزان قیمت
۳- سرعت لایه نشانی نسبتاً بالا
۴- پایین بودن دمای محفظه در حین فرآیند (امکان لایه نشانی بر قطعات پلاستیکی)
معایب:
۱- تراکم کم پوشش به دلیل پایین بودن انرژی مواد تبخیر شده (۰.۱- ۰.۵ الکترون ولت)
۲- چسبندگی ضعیف مواد لایه نشانی شده به زیرلایه
۳- عدم امکان لایه نشانی مواد فلزی دیرگداز
۴- امکان حضور ناخالصی جزئی بوته به داخل پوشش
با وجود چسبندگی ضعیف این روش، استفاده از این پوشش در مواردی که قطعه پوشش شده در دسترس و در مواجهه با سایش قرار نداشته باشد مناسب و کاربردی می باشد. به عنوان مثال پوششدهی جداره داخلی کاسه چراغ اتومبیل با آلومینیم امکان بازتاب بیشتر نور را فراهم می سازد.
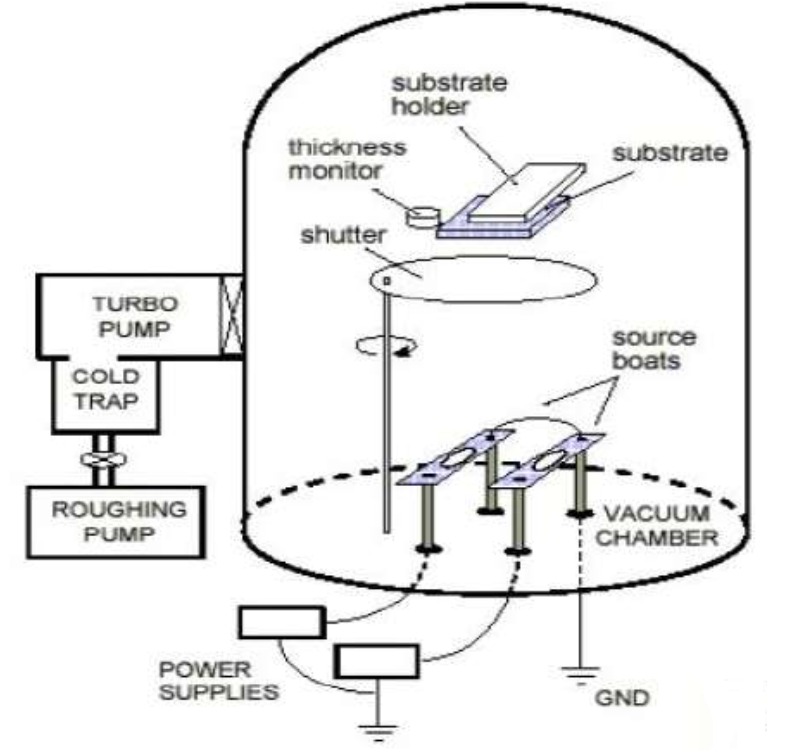
شکل۱- روش تبخیر حرارتی
۲-۱- تبخیر با باریکه الکترونی Electron Beam Evaporation:
با توجه به عدم امکان لایه نشانی مواد دیرگداز و مواد سرامیکی با روش تبخیر حرارتی، روش تبخیر با استفاده از باریکه الکترونی مطرح شده است. در این روش بعد از اعمال جریان بالا به فیلامان تنگستن و داغ شدن آن، الکترون تولیدی به وسیله یک میدان الکتریکی کانونی شده و با پیمودن زاویه ۲۷۰ درجه ای بر سطح ماده هدف که در بوته مخصوصی قرار گرفته است، تابانیده می شود. به دلیل انرژی بسیار بالا باریکه الکترونی امکان تبخیر مواد دیرگداز و مواد سرامیکی از جمله مواد نیمه هادی و دی الکتریک میسر خواهد بود. باریکه الکترونی صرفاً ناحیه کوچکی از زیرلایه را ذوب و تبخیر نموده و موجب تشکیل لایه ای با خلوص بالا بر روی زیرلایه می شود.
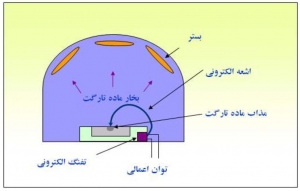
شکل۲- روش تبخیر باریکه الکترونی
مزایا:
۱- امکان تبخیر کلیه مواد دیرگداز و سرامیکی
۲- خلوص بالاتر نسبت به روش تبخیر حرارتی
۳- عدم نیاز به حضور گاز خنثی در حین لایه نشانی(فشار در محدوده ۵- ۱۰ تا ۶-۱۰ تور)
۴- سرعت لایه نشانی نسبتا بالا
معایب:
۱- به دلیل تفاوت در نقطه ذوب و تبخیر مواد، عدم امکان دستیابی به استوکیومتری دقیق در مواد مرکب و آلیاژی
۲- تجهیزات گران قیمت تر نسبت به روش تبخیر حرارتی
با توجه به امکان لایه نشانی مواد با نقطه ذوب بالا، این روش در صنعت الکترونیک، اپتیک و صنعت نیمه هادی مورد توجه قرار گرفته است. همچنین با توجه به سرعت بالای لایه نشانی آن و نوع سازوکار لایه نشانی(رشد ستونی)، در دهه اخیر برای اعمال پوششهای سد حرارتی TBC برای پوششدهی پره توربین در صنعت هوایی به مرحله تجاری درآمده و توسط شرکتهایی معتبر در سراسر دنیا مورد استفاده می باشد.
۳-۱- تبخیر به روش قوس کاتدی Cathodic Arc Evaporation:
در فرآیند Arc PVD، در محیط خلا تخلیه الکتریکی بین دو الکترود (آند و کاتد) اتفاق می افتد. متوسط جریانی لازم است تا یکی از الکترودها یونیزه شده و تبخیر شود. در این روش، تبخیر ممکن است بر کاتد یا بر آند صورت گیرد. روش PVD قوسی کاتدی از جمله روش هایی است که هم اکنون در صنعت ایران مورد استفاده تجاری قرار می گیرد. در این روش تشکیل قوس الکتریکی مانند سامانه جوشکاری می باشد که بعد از برقراری جریان بالا، سطح تارگت (کاتد) یونیزه شده و اتم های یونیزه به سمت قطعه حرکت می کند. در صورت حضور گاز واکنشی از جمله N2 در اتمسفر محفظه، موجب تشکیل ترکیب نیترید فلزی TiN روی قطعه خواهد شد.
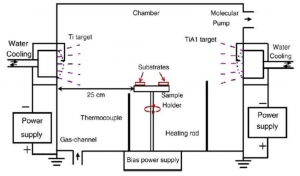
شکل۳- شماتیک فرآیند تبخیر به روش قوس کاتدی
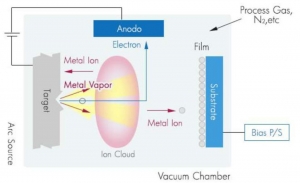
شکل۴- تشکیل پلاسما و ایجاد پوشش در روش بخیر به روش قوس کاتدی
مزایا:
۱- امکان لایه نشانی کلیه فلزات و تشکیل نیترید و کاربید فلزات
۲- به دلیل بالا بودن انرژی اتمهای تبخیری، چسبندگی و تراکم مناسب پوشش به زیرلایه
۳- سرعت لایه نشانی نسبتاً بالا
با استفاده از این روش، امکان لایه نشانی قالبها، ابزارها و قطعات صنعتی در مقیاس تجاری وجود دارد. همچنین از دیگر کاربردهای این روش برای ایجاد پوششهای تزئینی با رنگهای متنوع می باشد.
معایب:
۱- به دلیل ماهیت فرآیند، حضور ماکروذرات سبب ایجاد نقص در پوشش می شود
۲- تغییر جزئی در ترکیب استوکیومتری مواد آلیاژی
۳- عدم استفاده از تارگتهای نارسانا و نیمه هادی در این روش
۲- کندوپاش(Sputtering):
فرآیند کندوپاش، شامل کندن اتم به وسیله گاز کندوپاش کننده (مانند گاز آرگون) از سطح ماده هدف و نشاندن آن بر زیرلایه است. در کندوپاش، پلاسما نقش بسزایی در کندن اتم از سطح دارد. مراحل مختلفی که در این روش شکل می گیرد به شرح زیر است:
۱- یونیزه شدن اتمهای گاز آرگون به دلیل وجود اختلاف پتانسیل بالا بین کاتد و آند خواهد شد.
۲- یونهای آرگون مثبت به شدت به سمت پتانسیل منفی که محل قرارگیری ماده هدف است برخورد می کند.
۳- یونهای آرگون ماده هدف را بمباران کرده که سبب کنده شدن مواد و پرتاب به سمت زیرلایه خواهد شد. بهره کندوپاش فلزات با یکدیگر متفاوت است به عنوان مثال فلزی مانند نقره بیشتر و سریعتر از تیتانیم می باشد (بهره کندوپاش نسبت اتمهای کنده شده و یونهای اصابت کرده می باشد).
۴- در نتیجه لایه نازک مورد نظر بر زیرلایه تشکیل می شود.
۵- همچنین الکترون های ثانویه و آزاد موجود در محفظه با اتمهای آرگون برخورد نموده و یون های بیشتری تولید می کند که موجب تولید بیشتر پلاسما برای فرآیند کندوپاش خواهد شد.
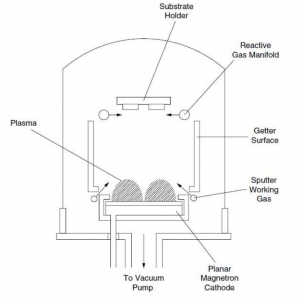
شکل ۵- شماتیک کلی از روش کندوپاش
با توجه به نوع پتانسیل اعمالی و گازهای واکنشی اضافی، انواع مختلفی از فرآیند کندوپاش وجود خواهد داشت. انواع روشهای فرآیند کندوپاش عبارتند از:
۱- DC Sputtering (برای لایه نشانی فلزات)
۲- AC Sputtering یا RF (برای لایه نشانی فلزات و غیر فلزات)
۳- Reactive Sputtering (برای لایه نشانی ترکیبات نیتریدی، کاربیدی و اکسیدی)
۴- Magnetron Sputtering (برای لایه نشانی با راندمان بیشتر)
۵- HiPIMS (High power impulse magnetron sputtering) (برای لایه نشانی همه موارد فوق الذکر با راندمان بیشتر)
منبع: مهندسی نانو پوششهای سخت و مقاوم؛ دکتر حسن علم خواه