اساس روش “پلاسما اسپری – رسوب نشانی فیزیکی از فاز بخار” یا همان PS-PVD، فناوری پاشش پلاسما با فشار کم (LPPS) است که چندین سال است در صنعت به خوبی شناخته شده است در این مطلب به بررسی مزایای این روش در مقایسه با دیگر روش های رایج پوشش دهی خواهیم پرداخت.
یکی از ویژگی های مشترک در فرآیندهای اسپری حرارتی (PS) این است که ایجاد پوشش توسط اسپری کردن مواد پوشش ذوب شده یا نیمه مذاب انجام می شود. فرآیندهای رایج اسپری پلاسما در خلاء معمولاً در فشارهای بالاتر از 3 کیلو پاسکال کار میکنند . بر خلاف فناوری اسپری حرارتی، فشار کاری فرآیندهای رسوب بخار فیزیکی (PVD) بسیار کم است و می تواند از تا متغیر باشد.
در PVD، مواد پوشش به طور مستقیم از یک ابر بخار بر روی زیرلایه متراکم می شوند. این خصوصیت باعث می شود تا بتوان پوشش هایی با ویژگی هایی تولید کرد که هنوز با هیچ یک از فرآیندهای اسپری حرارتی شناخته شده قابل دستیابی نیست.
پوششهای PVD بسیار همگن، نازک، متراکم، سخت، ضد گاز و دارای ریزساختارهای مهندسی شدهای هستند.
با این وجود، معایب فرآیندهای عادی PVD، هزینه های سرمایه گذاری بالا و نرخ رسوب نشانی پایین است. به همین دلیل، این فناوری عمدتاً برای تولید انبوه فیلم نازک یا تولید پوششهای ضخیم عایق حرارت TBC روی قطعات حساس مانند پرههای توربین موتور هواپیما استفاده میشود. یکی دیگر از محدودیت های روش PVD معمولی این است که این روش فرآیندی موثر بر خط دید است. یعنی فقط سطوحی از قطعه که در معرض خط دید مستقیم منبع تولید پوشش قرار دارند می توانند پوشش دهی شوند. بنابراین، پوشش دهی اجزایی با هندسه پیچیده و نواحی قرار گرفته در سایه به طور یکنواخت به این روش بسیار دشوار خواهد بود.
ترکیب مزایای روش پاشش حرارتی، یعنی کیفیت پوشش بالا، نرخ رسوب بالا و هزینه های سرمایه گذاری پایین با پوشش های رسوب نشانی از فاز بخار با استفاده از فناوری اسپری پلاسما چالشی است که می تواند یک فرآیند استاندارد اسپری پلاسمای فشار پایین (LPPS) را به یک فرآیند دارای قابلیت رسوب نشانی از فاز بخار که به آن PS-PVD گفته می شود، تبدیل نماید .
PS-PVD قادر است پوشش را همزمان با دو روش ذوب کردن مواد اولیه و در ادامه ایجاد لایهای از لکههای مایع روی سطح و همچنین با تبخیر کردن مواد اولیه و رسوب نشانی از فاز بخار، رسوب دهد. بنابراین، فرآیند PS-PVD شکاف بین فنآوریهای متداول رسوب نشانی فیزیکی از فاز بخار (PVD) و فرآیندهای استاندارد اسپری حرارتی را پر میکند.
برخلاف سایر فناوریهای PVD، این فرآیند توانایی پوشش دادن مناطقی را دارد که در محدوده خط دید منبع پوشش قرار نمیگیرند. این مزیت، امکان پوشش دهی کامل قطعاتی را که دارای هندسه پیچیده و مناطق درون سایه هستند، مانند تیغه های پیچیده توربین یا پره های دوگانه پمپ های کارتریجی را فراهم می کند.
PS-PVD بر اساس فناوری های LPPS, VPS و LVPS طراحی شده که همه تحت شرایط فشار کاهش یافته و معمولاً در اتمسفر گاز آرگون عمل میکنند. فشار کاری رایج فرآیندهای پاشش حرارتی خلاء بین 3 تا 20 کیلو پاسکال است که امکان رسوب پوشش های با محدوده ضخامت معمولی را فراهم میکند. کاهش دادن فشار محیط، طول ستون پلاسمای ایجاد شده را افزایش می دهد. ستون بزرگتر باعث ایجاد محدوده اسپری بزرگتری روی سطح قطعه می شود. سرعت ذرات و دما می تواند به طور همگنتری در سطح مقطع ستون پلاسما توزیع شوند(شکل 1). این اجازه می دهد تا پوشش هایی با توزیع ضخامت همگن حتی روی قطعات با هندسه پیچیده تولید شود.
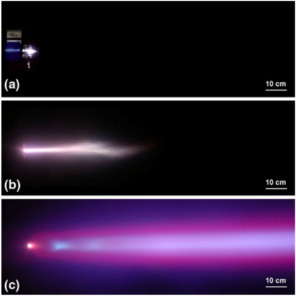
شکل 1: تصاویری از توسعه ستون پلاسما در فشار های مختلف: (a): 95 کیلو پاسکال، (b):5 کیلو پاسکال و (c): 0.1 کیلوپاسکال
یکی از ویژگی های اصلی مورد انتظار از پوشش PS-PVD، تولید یک سد حرارتی TBC مقاوم در دمای بالا مشابه پوشش های EB-PVDاست. هدف اصلی این است که پوششی با ساختار ستونی رسوب نشانی شود که بتواند خواصی از جمله تحمل کرنش بالا، مقاومت مناسب در برابر سایش و رسانایی حرارتی پایین را به دست آورد.
انواع مختلفی از ریزساختارها را می توان با تغییر شرایط فرآیند تولید کرد. شکل2 دو پوشش ساخته شده.در شکل2، (a) یک پوشش متخلخل است. ساختار ستونی که در شکل 2، (b) نشان داده شده است با تنظیم نرخ تغذیه پودر پایین، مخلوط خاصی از آرگون و گازهای پلاسمای ثانویه و با داشتن فاصله اسپری کردن زیاد حاصل میشود.
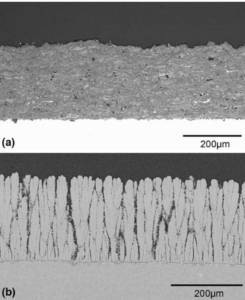
شکل 2: پوشش عابق حرارتی با ترکیب 7YSZ دارای ریز ساختار (a): پاششی و (b) ستونی
از روش طیف سنجی نوری (OES) برای بررسی تاثیر تغییر پارامترهای پلاسما بر مواد تزریقشده در داخل جت پلاسما استفاده می شود. شکل 3، (a) طیف جت پلاسما را با پودر YSZ تزریق شد است رانشان می دهد که شدت خطوط طیف بدست آمده از گونه YSZ کم است نشان می دهد فقط مقدار کمی از مواد پوشش تبخیر شده اند.
در شکل 3،(b)، طیف بدست آمده افزایش کلی خطوط طیفی YSZ را نشان می دهد خطوط طیفی مربوط به گونه های مختلف موجود در YSZ، یعنی زیرکونیوم و ایتریم است. در اینجا، ماده تزریق شده بیشتر تبخیر شده است که اجازه رشد پوششی با ساختار ستونی را می دهد. شدت خطوط طیف بدست آمده از گونه YSZ کم است، که نشان می دهد فقط مقدار کمی از مواد پوشش تبخیر شده اند.
![]() |
![]() |
شکل 3: طیف سنجی OES از جت پلاسما حاوی پوشش عابق حرارتی با ترکیب 7YSZ دارای ریز ساختار (a): پاششی و (b) ستونی
|
شکل 4: تصویر میکروسکوپی از مقطع عرضی پوشش EB-PVD از جنس 7YSZ
|
شکل 4 یک ریزساختار TBC معمولی را در مقطع عرضی نشان می دهد. در مقابل این ساختار حجیم و فشرده ستونی و دارای نقوص کم، ستون های تولید شده توسط PS-PVD سوزن هایی ظریف با تراکم نقص بالا و مقدار زیادی تخلخل داخلی میباشند. در شکل 5 نمونه ای از ساختار ستونی معمولی PS-PVD با ضخامت لایه نشان داده شده است. شکل 6 مقاومت در برابر سایش ریزساختارهای مختلف PS-PVD را همراه با پوشش های APS و EB-PVD به عنوان مرجع نشان می دهد. مطابق این شکل، در مقایسه با EB-PVDمقاومت سایشی PS-PVD پایین تر است. این را می توان به ساختار سوزنی ظریف و شکاف های بین ستونی گسترده توجیه نمود که استحکام مکانیکی پایینی برای پوشش ایجاد می کند. با این وجود بهینه سازی پارامتر های پوشش منجر به افزایش نسبی مقاومت به سایش نمونه ی “” در شکل 6 شده است. ریز ساختار ستونی بهینه شده () نیز در شکل 7 نمایش داده شده است.
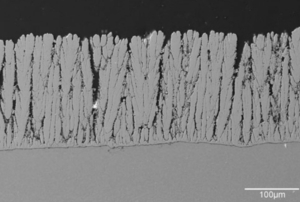
شکل 5: پوشش TBC ستونی با روش PS-PVD بر روی پوشش MCrAlY رسوب نشانی شده است.
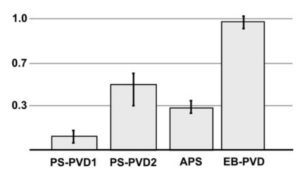
شکل 6: مقاومت نسبی در برابر سایش پوشش های مختلف تولید شده به روش PS-PVD (، بهینه نشده، ، بهینه شده)، APS و EB-PVD به عنوان مرجع
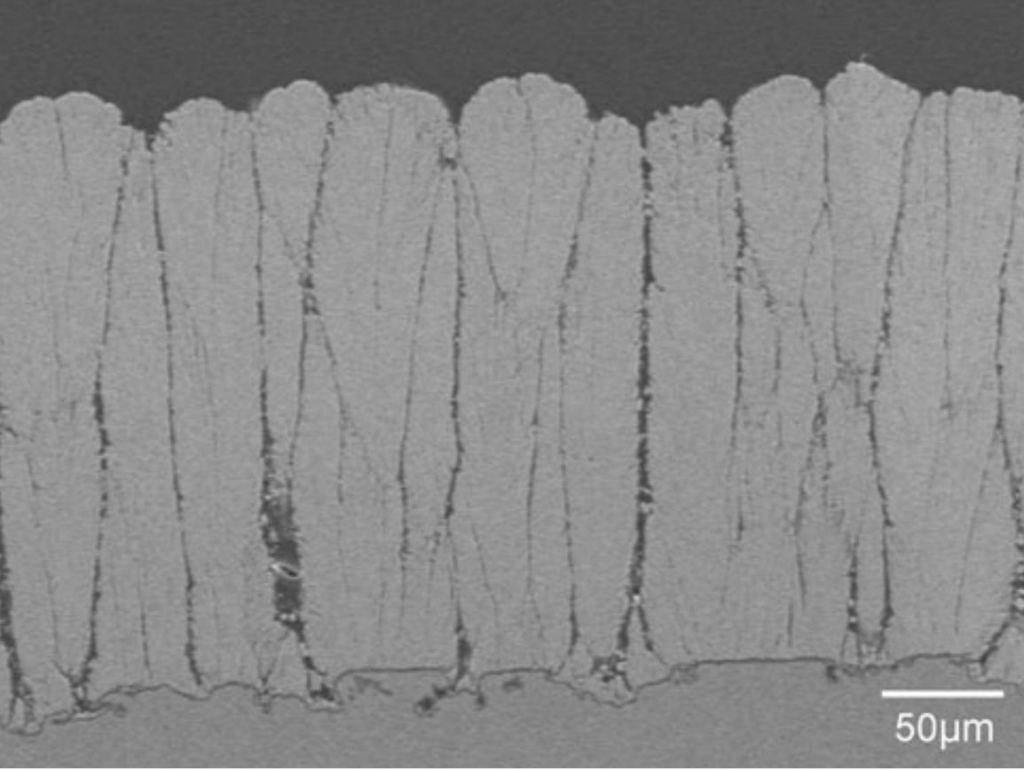
شکل7: ساختار TBC ستونی اعمالی به روش PS-PVD بهینه شده بر روی یک پوشش MCrAlY
کاربرد روش PS-PVD در پوشش دهی قطعات پیچیده مانند پره های توربین و پمپ می باشد که در شکل 8 نمونه تیغه دوبل پوشش دهی شده به این روش و با ماده YSZ قابل مشاهده است. با اندازه گیری ضخامت پوشش در نقاط مختلف این دو تیغه (شکل9) مشخص می گردد که پوشش در تمامی نواحی به طور یکنواخت و مناسب اعمال شده است و صخامت حداقلی 120 میکرومتری در تمامی نقاط اعمال شده است.
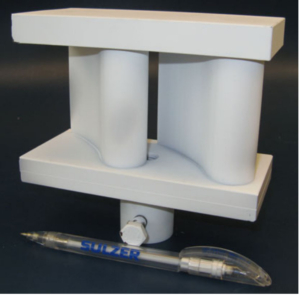
شکل 8 : نمونه تیغه دوبل پوشش دهی شده با YSZ با استفاده از روش PS-PVD
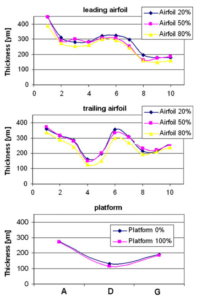
شکل 9: بررسی ضخامت پوشش در نواحی مختلف نمونه پوشش دهی شده در (بالا) پره جلویی (وسط) پره عقبی و (پایین) پایه.
از نتایج تست های فوق میتوان به این جمع بندی رسید که با استفاده از فناوری PS-PVD، پوشش دارای ریزساختار ستونی منحصربهفردی خواهد بود که تا کنون تنها با سایر فرآیندهای رسوبگذاری فاز بخار مانند EB-PVD به دست آمده است. با وجود این مورفولوژی، پوشش دارای ویژگی های خاصی خواهد بود که کاربرد آن در قطعات حساسی مانند پره های توربین گازی است.
توانایی PS-PVD برای پوشش مناطق سایه دار و مناطقی که در محدوده دید منبع پوشش قرار نمی گیرند بسیار بالاست. این فناوری پتانسیل بالایی برای ارائه راهحلهای پوششدهی جدید غیر مستقیم و استفاده از آنها در افزایش سود اقتصادی تولید کننده ارائه میدهد.
پوششهای تولید شده به روش PS-PVD بسیار مقاوم به کرنش هستند و رسانایی حرارتی بسیار کمی را ارائه میدهند. همچنین مقاومت در برابر سایش کمتر از پوشش های EB-PVD است اما در حدود پوشش های استاندارد APS TBC با تخلخل 15 درصد می باشد که عدد قابل قبولی است.