چکیده
ساختارهای نانو و نانوکامپوزیت هایی که به روش PVD به عنوان پوشش استفاده شده باشند، به علت خواص فیزیکی و شیمیایی استثنایی بسیار مورد توجه قرار گرفته اند. فبلم های نازک و پوشش های PVD دارای خواص بهبود یافته ای از قبیل مقاومت به خوردگی، مقاومت به رفتگی و سختی و اصطکاک مناسب هستند. فرآیند های پوشش دهی PVD با اهداف کاربردی بسیاری از قبیل صنعتی، اتوموبیل سازی و هوافضا در حال توسعه هستند. در این مقاله هدف بررسی و مرور کاربردهای مختلفی است که توسط پژوهشگران دیگر در خصوص استفاده از پوشش های PVDمعرفی شده اند.
مقدمه
در سال های اخیر علم پوشش و فیلم نازک به یکی از مهم ترین زمینه های تحقیقاتی تبدیل شده است. اهمیت پوشش ها و تولید مواد جدید برای صنعت منجر به پیشرفت و ابتکار قابل توجهی در فناوری های فیلم و پوشش های نازک شده است. در حال حاضر، با افزایش ناگهانی پیشرفت در زمینه های میکروالکترونیک، اپتیک و فناوری نانو توسعه ی فیلم و پوشش های نازک با ضخامتی در محدوده یک تا چند میکرون فراگیر شده است. این پوشش ها در چندین شاخه ی ساخت و تولید ضروری هستند ازجمله: حفاظت از رفتگی و پوشش های عایق حرارتی، بهبود طول عمر ابزار و حفاظت از مواد در برابر آثار مخرب اتمسفری و حرارتی. درحال حاضر، نیاز به پوشش دهی مواد و وسایل مختلف که دائما در حال تغییر و افزایش است منجر به ایجاد فرصت هایی برای توسعه فرآیند ها، مواد اولیه و فناوری های جدید شده است. بنابراین انجام فعالیت های تحقیقاتی گسترده، با هدف توسعه توانایی های بالقوه موجود در خواص فیزیکی و شیمیایی ریزساختار ها و بهبود عملکرد پوشش ها در کاربردهای مختلف، ضروری است.
فرآیندهای پوشش دهی بسیار متنوعی وجود دارند که همگی از فرآیندهای مطلقا شیمیایی یا مطلقا فیزیکی سرچشمه گرفته اند. مهم ترین فرآیندهای پوشش دهی بر پایه روش های شیمیایی در فاز مایع، روش های شیمیایی در فاز گاز، تخلیه تابشی، و روش های تبخیری هستند. اخیرا، فرآیند های نوینی با استفاده از ترکیب چند فرآیند پوشش دهی مختلف ساخته شده اند. ترکیب کردن چند روش اجازه می دهد تا طراحی و کنترل ریزساختار و خواص پوشش ها راحت تر و بهتر باشد.
فناوری PVD تولید پوشش های با کیفیت را تضمین می کند و تا کنون با استفاده از روش های مرسوم عملیات سطحی به کیفیت این فناوری دستیابی نشده است. در یک سال اخیر، توجه ویژه ای به فناوری PVD به جهت سازگاری با محیط زیست معطوف شده است. این فناوری به علت براورده کردن نیاز های صنعتی مواد و پوشش ها نیز مورد توجه است. این توجه با کمک توسعه های جدید در تجهیزات و نوع لایه های ایجاد شده که به خواص و عملکرد بهتر منجر شده است، بدست آمده است.
مواد و پوشش های صنعتی عمدتا در معرض دماهای بالای کاری قرار دارند که این اتفاق می تواند به علت دمای بالای محیط و یا حرارت ایجاد شده بر اثر اصطکاک باشد. به عنوان مثال، پوشش های نازک سخت PVD معمولا روی ابزار برش اعمال می شوند. این ابزارها در معرض تنش های بالا و حرارت ناشی از اصطکاک هستند. حرارت دیدن پوشش ممکن است اثرات موقت یا دائمی بر خواص آن داشته باشد. مشاهده شده است که سختی پوشش های PVD بر اثر حرارت دهی کاهش یافته و با سرد شدن مجدد، افزایش می یابد. اما سختی نهایی در نهایت به دلیل آسیب دائمی، کمتر از مقدار اولیه خواهد بود.
انواع پوشش دهی PVD
رسوب دهی فیزیکی بخار(PVD):
فرآیند PVD تحت خلاء شدید و دمایی بین ۱۵۰ تا ۵۰۰ درجه سلسیوس انجام می شود. باتوجه به مشاهدات، پس از شروع به توسعه ی آهسته تر در مقایسه با CVD، تکنیک های فیزیکی (PVD) در اواخر دهه ۷۰ میلادی واقعا رشد کردند. درسال ۱۹۷۶ تنها یک ترکیب (TiN) به این روش به عنوان پوشش استفاده می شد. این عدد در سال ۱۹۸۳ به سه ترکیب (TiCn و CrN اضافه شدند) افزایش یافت و تا سال ۲۰۰۳ بیش از ۴۰ ترکیب به این روش رسوب دهی شدند و این عدد در سال ۱۰۱۱ به بیش از ۱۰۰ ترکیب رسید.
- تبخیر حرارتی(TE)
الف. رسوب دهی لیزر پالسی (PLD)
یک اشعه لیزر به صورت پالسی بر روی سطح یک جامد هدف متمرکز می شود. جذب بالای تابش الکترومغناطیسی توسط جامد منجر به تبخیر سریع مواد هدف می شود. مواد تبخیر شده شامل گونه های به شدت برانگیخته و یونیزه شده هستند. درصورتی که تبخیر در محیط خلا انجام شود (مانند شکل ۱) ذرات تبخیر شده به صورت یک ستون پلاسمای درخشان در جلوی سطح مورد نظر برای نشاندن رسوب ظاهر می شوند. با دست بردن در شرایط رسوب، در این روش می توان به تولید ذرات نانو با ابعاد مورد نظر و رسوب دهی آنها روی زیرلایه دست یافت.
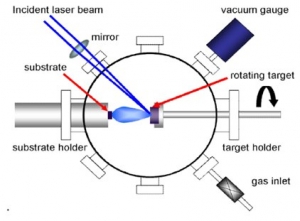
شکل ۱: رسوب دهی لیزر پالسی
ب. رسوب بخار فیزیکی پرتو الکترون(EB-PVD)
در این فرآیند، ماده ی مورد نظر به وسیله ی یک پرتو الکترونی حاصل شده از فیلامان تنگستنی در شرایط خلاء بمباران می شود. پرتو الکترون موجب بخار شدن اتم هایی از سطح ماده شده و در ادامه این اتم ها به شکل رسوب جامد بر روی سطح مورد نظر درون محفظه خلاء نشانده می شوند و لایه نازکی از مواد آند را همانند شکل 2 روی آن می نشانند. یکی از مزایای واضح این روش آن است که در آن اجازه داده می شود تا انرژی در حین گرمایش هدف به منبع نیز منتقل شود و بازدهی آن در رسوب دهی مواد خالص بخار شده روی زیرلایه بسیار بالاست. همچنین نرخ رسوب دهی در این فرآیند می تواند از مقادیر بسیار کم و درحد nm/min ا تامقادیر بالای چند میکرومتر در دقیقه متغیر باشد. بازده مصرف مواد نیز در مقایسه با روش های دیگر بالاست و این فرآیند بر روی ساختار و مورفولوژی فیلم تشکیل شده نیز کنترل دارد.
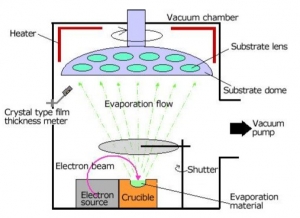
شکل ۲: رسوب دهی با پرتو الکترونی
این روش به دلیل سرعت رسوب دهی بالا، پتانسیل استفاده برای اعمال پوشش های عایق حرارت و ضد سایش مورد مصرف در صنایع هوافضا و ابزار سازی، پوشش های سخت در صنایع الکترونیک و فیلم های اپتیک برای صنایع نیمه رسانا را داراست.
- رسوب دهی پاششی
الف) پاشش با اشعه یونی
در روش پاشش با اشعه یونی از یک منبع یون برای تولید اشعه یونی نسبتا متمرکزی استفاده می شود که به سمت قطعه هدفی که از آن پاشش انجام می شود نشانه گیری شده است. منبع یونی شامل یک آند و یک کاتد است. اعمال ولتاژ بالای میدانی در حدود kV2-10 به آند میدان الکترواستاتیکی در داخل منبع یونی ایجاد میکند که الکترون ها را در اطراف یک نقطه زینی در مرکز منبع محصور می کند. با تزریق گاز آرگون به درون منبع، میدان قوی الکترونی گاز را یونیزه می کند و درون منبع، پلاسما ایجاد می شود. در ادامه یون ها از منطقه آند شتاب گرفته و به سمت روزنه خروجی (کاتد) حرکت می کنند و یک اشعه موازی سازی شده یونی ایجاد می شود. اشعه حاصل به مواد هدف حمله کرده و همانند شکل ۳ این مواد را به روی زیرلایه پاشش می دهد. پوشش دهی دیواره های داخلی تیوب ها و لوله ها چسبندگی خوب و رسوب فشرده ای دارد اما اگر قطر لوله کم باشد یا طول آن زیاد باشد، استفاده از این روش با پیچیدگی مواجه خواهد بود.
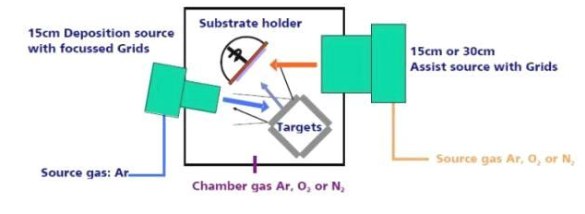
شکل ۳: پاشش با اشعه یونی
ب) پاشش مگنترونی
پاشش مگنترونی یک فرایند PVD است که در آن پلاسما ایجاد شده و یون های دارای بار مثبت آن به کمک میدان الکتریکی و مغناطیسی به سمت الکترود دارای بار منفی یا همان “هدف”، شتاب می گیرند. یون های مثبت به واسطه پتانسیل هایی در محدوده صدها تا هزاران الکترون ولت شتاب گرفته و با نیروی کافی برای بیرون راندن اتم های هدف به الکترود منفی برخورد می کنند. همانند شکل ۴، این اتم ها از سطح هدف به شکل توزیع کسینوسی پراکنده شده و بر روی سطوحی که در محدوده پاشش مگنترونی هستند می نشینند. در موارد رسوب دهی کربنی، توان پاشش مگنترونی ثابت نگه داشته می شود.
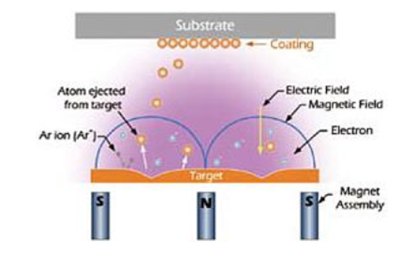
شکل ۴: پاشش مگنترونی
- رسوب تبخیری قوسی
الف. رسوب قوسی در خلاء
رسوب دهی قوسی در خلاء یا همان PVD قوسی، از دیگر تکنیک های رسوب دهی فیزیکی بخار است که در آن از یک قوس الکتریکی برای بخار کردن مواد از سطح هدف کاتدی استفاده می شود. مواد بخار شده در ادامه بر روی یک زیرلایه نشسته و فیلم نازک تشکیل می دهند. به کمک این فناوری می توان فیلم های فلزی، سرامیکی و کامپوزیتی را رسوب دهی کرد.
فرآیند تبخیر با حمله ی یک قوس با جریان بالا و ولتاژ کم به سطح هدف آغاز می شود. در این حالت، در منطقه ای کوچک روی سطح کاتد هدف، که به نام “نقطه کاتدی” شناخته می شود، انرژی متمرکز شده و دما به شدت بالا می رود ( حدود ۱۵۰۰۰ درجه سانتیگراد). این اتفاق باعث می شود مواد تبخیر شده کاتد از آن نقطه با سرعت بسیار بالایی (km/s۱۰) به خارج پرتاب شوند و حفره ای روی سطح کاتد باقی بگذارند. نقطه ی تنها برای چند لحظه فعال است و در ادامه قوس بر روی نقطه دیگری در نزدیکی نقطه قبلی متمرکز خواهد شد. این رفتار باعث می شود حرکت ظاهری قوس ایجاد شود.
مطابق شکل ۵، از آنجایی که قوس اساسا یک رسانای حاوی جریان است، استفاده از میدان الکترو مغناطیسی می تواند آن را روی سطح کاتد به حرکت در بیاورد و بدین ترتیب کل سطح به مرور زمان خورده شود.
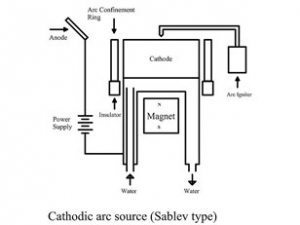
شکل ۵ رسوب قوسی در خلاء
ب. رسوب قوسی فیلتر شده
منبع تولید رسوب روش قوس کاتدی فیلتر شده در خلاء ، پلاسمای یونیزه شده است. در این روش جریان قوس می تواند تا A300 باشد که برای رسوب دهی عناصر مختلف روی سطح عالی است. پلاسمای یونیزه شده به کمک میدان الکترومغناطیسی هدایت شده و با عبور از فیلتر ذرات درشت90 درجه، رسوبی بدون نقص و عیوب را روی زیرلایه می نشاند. از این روش برای تولید پوشش های چگال، محافظ، تزئینی، نانو کامپوزیت، نانو ساختار و چندلایه استفاده می شود. چیدمان شماتیک این روش در شکل 6 مشخص شده است. فرآیند رسوب قوسی کاتدی فیلتر شده (FCVAD) با جلوگیری از رسوب بسیاری از عوامل باعث می شود کنترل بهتری بر نحوه رشد پوشش PVD روی زیرلایه وجود داشته باشد.
- کاشت یون
رسوب اشعه یونی (IBD)
رسوب اشعه یونی (IBD) از یک منبع فعال و وسیع یونی که به طور پیوسته بر روی یک هدف پاششی فلزی یا دی الکتریک متمرکز شده است استفاده می کند.
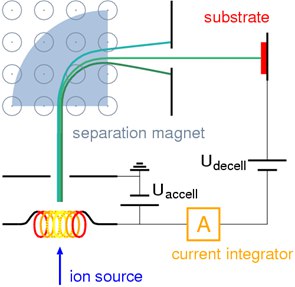
شکل ۶ نحوه عملکرد سیستم IAD
مواد پاشیده شده از هدف بر روی یک زیرلایه رسوب کرده و فیلم نازک تشکیل می دهند. در کنار این اتفاق، در بسیاری از کاربرد ها منبع یونی کمکی یا IADوجود دارد (شکل ۶) که بر روی زیرلایه متمرکز شده و یون های متحرک نجیب یا فعال را روی سطح فیلم درحال رشد قرار می دهد. IAD استحکام، پایداری، خواص دی الکتریک و خواص اپتیک فیلم های اکسید و نیترید فلزی را به خوبی افزایش می دهد. هر یون یک اتم یا مولکول است بنابراین مقدار یون انباشت شده روی سطح برابر با انتگرال جریان بر حسب زمان خواهد بود و به این مقدار دُز گفته میشود. از آنجا که در کاشت یون جریان در حد میلیآمپر است، دز یون کاشتهشده مقدار کمیست.انرژی یونهای تابشی پیرامون ۱۰ تا ۵۰۰ کیلو الکترونولت است. انرژی یون، جنس ماده یون و همچنین نوع زیرلایه تعیینگر میزان عمق نفوذ یون
روی سطحاند و این مقدار عموما بین ۱۰ نانومتر تا ۱ میکرومتر است.