پوشش دهی PVD چند لایه به منظور حفاظت در مقابل سایش
خلاصه
فناوری PVD به خوبی برای آشنایی با مفاهیم پوشش های جدید و پیشرفته مانند پوشش های گرادیانی، پوشش های نیمه پایدار، پوشش های چند جزئی و پوشش های چند لایه یا ابر شبکه مناسب است. از بین این پوشش ها، پوشش چند لایه امیدوارکننده ترین نوع است زیرا بسیاری از نیازها را (به عنوان مثال چند منظوره بودن، تنش پسماند کم، چسبندگی مناسب به زیرلایه فلزی، نسبت سختی به چقرمگی مناسب و ضرایب اصطکاک پایین) برای کامپوزیتی که در معرض شرایط سایش پیچیده قرار دارد، برآورده می کند. به علاوه، این پوشش اجازه می دهد تا مواد نیمه پایدار و چند جزئی در یک چیدمان چند لایه تنظیم شده قرار بگیرند و بدینگونه، انواع چیدمان لایه ای مختلف به طور همزمان قابل بررسی می باشد. یک طراحی کاربردی و ساختاری با در نظر گرفتن انتخاب مواد برای هر لایه، تنظیم حجم فصل مشترک و بهینه سازی ترتیب و ضخامت هر لایه، امکان تنظیم دقیق خواص و عملکرد را فراهم می آورد. مواد کووالانسی یا یونی مانند B4C ، SiC ، Si3N4 یا Al2O3 را می توان به عنوان لایه های میانی در چیدمان چند لایه معرفی کرد. آنها باعث افزایش سختی و استحکام در دمای بالا بدون کاهش چسبندگی یا سختی پوشش می شوند. نتایج جدید در مورد ساخت، ویژگی ها و کاربردهای پوشش های چند لایه بر پایه TiC / TiN در این پژوهش ارائه شده است.
۱. مقدمه
امروزه مفاهیم پوشش دهی پیشرفته مانند پوشش های چندلایه، مواد پوشش چندجزئی سخت شده به کمک محلول سازی، مواد پوشش نیمه پایدار جدید، مواد پوشش نانوکریستالی یا فیلم های ابر شبکه اهمیت فزاینده ای در حفاظت از سایش تحت شرایط سخت و بارگذاری پیچیده دارند. در میان این پوشش های پیشرفته، پوشش های چند لایه با توجه به خواص، عملکرد و کاربردهای متنوع خود، به نظر منعطف ترین و امیدوار کننده ترین هستند.
مفاهیم مختلفی می توانند در یک پوشش ترکیب شوند و آن را برای کاربرد مشخصی تنظیم کنند. چنین حالتی در یک چیدمان چند لایه دارای تک لایه های نانوکریستالی نیمه پایدار درجه بندی شده مشهود است.
برای آشنایی با پیشینه و اهداف چندلایه ها ابتدا باید با مواد بالک آشنا شد. دانش ما در خصوص روابط موجود در ساختار، ریزساختار، خواص و خصوصیات کاربردی مواد از این طریق شکل گرفته و در طی سالهای متمادی افزایش یافته است. توسعه علمی در خصوص مواد صنعتی منجر به بهبود این مواد شده است. مبحث جدید فیلم های نازک و فناوری پوشش تا کنون پیشرفت زیادی نداشته و در آینده، عمدتا از راه های تجربی و عملی بهبود خواهد یافت. دانش اختصاصی موجود در زمینه مواد سرامیکی بالک و شکننده، می تواند به عنوان پایه ای برای توسعه مواد لایه ای استفاده شود. این دانش می تواند علی الخصوص برای بهینه سازی خواص مکانیکی و عملکرد در شرایط بارگذاری پیچیده مورد استفاده قرارگیرد.
مزایای پوشش های چند لایه امروزه در اکثر پوشش های تجاری CVD مورد استفاده قرار می گیرد. پوشش هایی که تا ۱۳ (عمدتا بین ۳ تا ۸) لایه داشته و معمولا دارای چیدمانی دلخواه از لایه هایی از جنس (TiC، TiN، TiCN) و Al2O3 هستند.
۲.مروری بر منابع
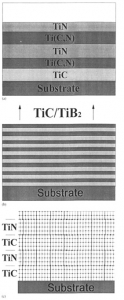
شکل۱: انواع مختلف پوشش های چند لایه:a) تعداد کمی تک لایه b) تعداد زیادی تک لایه ی نا هم ساختار c) تعداد زیادی تک لایه ی هم ساختار (ابر شبکه)
پوشش های چند لایه امروزه در زمینه های بسیاری مورد استفاده قرار می گیرند. پوشش های CVD که با هدف حفاظت از ابزار تولید می شوند، عمدتا چندلایه بوده و متشکل از ۳ تا ۱۳ لایه هستند. مزایای چند لایه بودن پوشش هم در ابعاد آزمایشگاهی و هم صنعتی به اثبات رسیده است. تا کنون پوشش های چند لایه PVD چه به صورتی که حاوی تک لایه هایی از جنس (TiC، TiN، TiCN) و (TiAlN) بوده و چه به صورت تعداد زیادی لایه از یک جنس (تا حدود ۲۰۰۰ لایه برای یک پوشش ۵ میکرونی)، تاکنون مورد بررسی قرار گرفته اند. در بررسی حالت دوم، رابطه ی مشخصی بین ترکیب پوشش، حجم فصل مشترک، خواص و مقاومت به سایش در شرایط برش ناپیوسته وجود دارد. به منظور دستیابی به پوشش هایی با سختی و چقرمگی مناسب در سطوح پیوندی فلزی/فلزی ، فلزی/ کووالانسی و فلزی/ یونی، مواد مناسب شناسایی شدند. اخیرا، خواص و عملکرد پوشش های چند لایه TiNx مورد بررسی قرار گرفته است و وابستگی آنها به ابر شبکه و دوره تکرار آن بررسی شده است. همچنین، ابر شبکه های رایج برای این پوشش های چندلایه مورد بررسی قرار گرفته اند.
۳.دسته بندی پوشش های چند لایه
برای درک بهتر ترکیب، خواص و عملکرد پوشش های چند لایه، تمایز میان پوشش های دارای تعداد کمی تک لایه، پوشش های دارای تعداد زیادی لایه ی غیر هم ساختار و پوشش های دارای تعداد زیادی لایه ی هم ساختار و همچنین امکان سنجی ایجاد اثر ابر شبکه ضروری است. در شکل یک، این موارد به طور شماتیک نشان داده شده است.
- پوشش هایی با تعداد محدودی تک لایه (شکل ۱ (a))
امروزه، عمده پوشش های آماده شده و مورد استفاده از این دسته هستند. پیش زمینه ی اصلی برای درک مفهوم این نوع پوشش این است که چطور رشد ستونی دانه را مختل کرده و چطور مواد مختلف را با یکدیگر ترکیب کنیم.
- پوشش هایی با تعداد زیادی از تک لایه های نا هم ساختار(شکل ۱ (b))
مقدار حجم فصل مشترک به عنوان مکانی برای اتلاف انرژی در این نوع پوشش اهمیت زیادی دارد. مختل کردن رشد ستونی دانه ها و ترکیب مواد لایه برای دستیابی به خواص و کاربرد های مختلف در اولویت های بعدی هستند.
- پوشش های ابر شبکه ای (شکل ۱ (c))
شرایط دستیابی به یک ابر شبکه ی واقعی شامل مواد لایه ی هم ساختار، پیوند های شیمیایی مشابه، شعاع های اتمی و فواصل شبکه ی نزدیک به هم و تنظیم ضخامت هر لایه در حدود ابعاد شبکه است. در صورت اعمال این شرایط، پوششی کاملا جدید و دارای خواص و ویژگی هایی مستقل از مواد تک لایه، مورد انتظار خواهد بود.
۴.جنبه های اصلی طراحی پوشش چند لایه
-
- ایده ها و اهداف کلی
ما از بررسی مواد بالک سرامیکی می دانیم که یک ساختار ریز چند فازی که دارای مقادیر بالایی از فصل مشترک است، معمولا چقرمگی و مقاومت به جوانه زنی ترک خوبی دارد. در پوشش های سخت، انتظارات مشابه سرامیک های شکننده است. به جز سختی، ما باید برای این پوشش ها چقرمگی مناسب فراهم کنیم چون ترک ها، شکستگی ها و چسبندگی نامناسب که به علت تنش های سنگین ایجاد می شوند، می توانند منجر به ناکارآمدی پوشش شوند. تولید فصل مشترک پوشش به کمک تشکیل نانوکریستال ها یا فیلم های چند لایه، می تواند به فائق آمدن بر این مشکلات کمک کند. از مطالعه تحقیقات انجام گرفته در مورد ارتباط مقاومت به سایش و مواد پوشش مشخص شده است که سایش، استحکام خستگی و شکست مواد وابسته به نسبت مناسب چقرمگی به استحکام (سختی) هستند. فصل مشترک ها در پوشش های چند لایه، محل اتلاف انرژی و انحراف ترک ها هستند که منجر به چقرمه شدن مواد لایه می شوند. آن ها همچنین ابعاد دانه و بافت را تنظیم می کنند و می توانند در استحکام دهی به پوشش از طریق تقویت تک لایه ها به خصوص در شرایط دمای بالا موثر باشند. به جز تنظیم نسبت فصل مشترک به دانه، درک ویژگی های دیگری از پوشش نیز از طریق درک مفهوم چند لایگی امکانپذیر است. بنابراین در طراحی پوشش چند لایه، طراحی کاربردی و طراحی ساختاری مناسبی مورد نیاز است (شکل ۲). در طراحی کاربردی میتوان موادی را با مقادیر مختلفی از کاهش دهی سایش یا هر خاصیت مورد نیاز با یکدیگر ترکیب کرد و در طراحی ساختاری می توان اندازه و شکل دانه ها، مقدار و ترکیب فصل مشترک و ضخامت هر لایه را تنظیم نمود و بدین ترتیب خواصی مانند نسبت سختی به چقرمگی یا استحکام در دماهای بالا را برای هر کاربرد مد نظر بهینه سازی کرد.
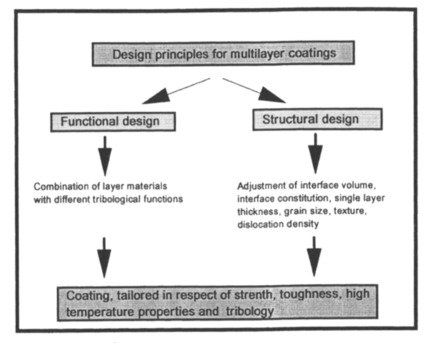
شکل ۲: اصول طراحی پوشش های چند لایه
- ترکیب فصل مشترک
ریز ساختار پوشش های چند لایه PVD، علاوه بر ترکیب و حجم مناطق فصل مشترک، به متغیر های دیگری مانند برهم کنش مواد با یکدیگر، ضخامت تک لایه، نرخ رسوب دهی، دمای زیر لایه، بمباران یونی و شرایط پلاسما وابسته است. بنابراین ارائه ی توصیفی دقیق و مختصر امکان پذیر نیست. با این حال می توان اظهاراتی کلی و عمومی در این زمینه بیان کرد: حجم، ترکیب و ساختار مناطق فصل مشترک در تعیین خواص و عملکرد پوشش مهم هستند. فصل مشترک های همدوس، نیمه همدوس و ناهمدوس با توجه به طبیعت و ساختار مواد دو سمت فصل مشترک نقش برجسته ای را در اتلاف انرژی و کاستن تنش ایفا می کنند. در اکثر موارد فصل مشترک ها مرزهای دقیق نیستند بلکه مانند شکل 3 مناطق مرزی توسعه یافته ای هستند. با داشتن اطلاعات در مورد فصل مشترک، می توان حجم فصل مشترک را در یک ماده ی چند لایه یا نانو کریستالی تخمین زد.
آنالیز AES فصل مشترک در پوشش های چند لایه، که توسط شرکت مگاترون انجام شد، گستره ای بین ۱ تا ۳ نانومتر را برای محدوده فصل مشترک تعیین کرد، که وابسته به مواد دو طرف آن است ( مثلا برای۱ TiC/TiB2 نانومتر، برای TiC/SiC ۲ نانومتر و برای SiC/B4C ۳ نانومتر). این مقدار برای یک پوشش ۱۰۰ لایه حدود ۲ تا ۶ درصد حجم و برای پوششی ۱۰۰۰ لایه به ضخامت 5 میکرومتر تا حد % ۶۰ حجم را به فصل مشترک اختصاص می دهد. فصل مشترک نسبت به مواد دو طرف خود متقارن نیست و عمدتا به ساختار ماده ای تمایل دارد که به عنوان زیرلایه عمل می کند. هنگامی که رسوب گذاری بر روی ماده ای آمورف صورت بپذیرد فصل مشترک تا سه برابر بزرگتر خواهد بود. در مورد رسوب گذاری روی مواد سخت فلزی مانند TiN، TiC و TiB2، محدوده فصل مشترک حدودا ۱ نانومتر است که مقدار نسبتا کمی می باشد.
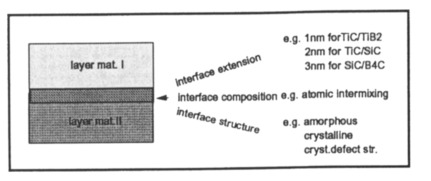
شکل ۳: مشخصه های ترکیب فصل مشترک در پوشش های چند لایه
حجم فصل مشترک می تواند به طور ساده شده، به عنوان یک فاز پیوند دهنده لایه ها در مواد سخت سرامیکی درنظر گرفته شود. برای کاهش شکنندگی، اتلاف کردن انرژی باید پیش از هر خاصیتی در محدوده فصل مشترک امکانپذیر باشد. مکانیزم های مختلفی برای این چقرمه سازی وجود دارند که در شکل ۴ نشان داده شده اند.
تصاویر SEM ناکارآمدی پوشش، عمدتا یک شکست پلکانی را در پوشش های چند لایه نشان می دهد که گواهی است بر منحرف شدن ترک در فصول مشترک. لازم به ذکر است که نه تنها مرز های بین هر لایه، بلکه مرز های داخل هر لایه که به علت تغییر جهت رشد دانه ها وجود دارند در ایجاد حجم موثر فصل مشترک نقش دارند. این امر در سامانه چند لایه TiC/TiB2 اثبات شده است.
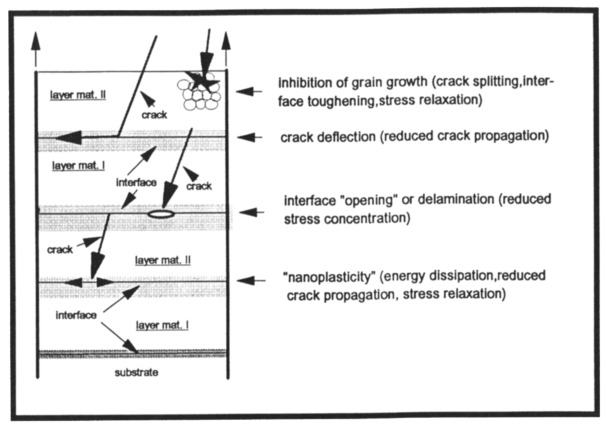
شکل ۴: مکانیزم چقرمه سازی در مواد چند لایه سرامیکی
برای تک لایه های همسان با ثوابت شبکه مشابه ماانند TiC و TiN، با افزایش تعداد لایه ها در ضخامت ثابت و یا کاهش ضخامت هر تک لایه، ویژگی های عمومی چند لایه ها در پوشش کم رنگ شده، ساختارهای ماژولار (یا ابر شبکه ها) بدست می آیند که از نظر ترکیب، ویژگی های ساختاری (مانند فواصل اتمی، ساختار نقص ها و چگالی نابجایی ها) و تنش یا کرنش (تنش های پسماند، تنش های حرارتی، تنش های همدوسی و میدان های کرنشی) تنظیم شده اند. نمونه های این حالت شامل TiC/TiN ، TiN/VN و یا TiN/NbN می شود.
در چیدمان چند لایه، لایه ی جدید تمایل دارد که با ساختاری نزدیک به لایه ی قبلی رشد کند. این اتفاق برای پوشش های چندلایه ای مانند TiC/TiB2 اثبات شده است.
۵.انتخاب مواد برای پوشش های چند لایه
مواد سخت متنوعی می توانند در قالب پوشش چندلایه با یکدیگر همراه شوند. مواد پوشش مناسب برای سایش را می توان با توجه به ویژگی های پیوند شیمیایی به سه گروه دسته بندی کرد: مواد سخت فلزی، کووالانسی و یونی( طبق شکل 5). این دستی بندی موجب درک بهتر ساختارهای متفاوت کریستالی و رفتار مواد به عنوان فیلم نازک در پوشش های چند لایه خواهد شد. مفهوم چندلایگی به خوبی برای ترکیب کردن مواد از دسته های یکسان و متفاوت قابل تنظیم است. در پوشش هایی که متشکل از موادی هستند که همگی متعلق به یک دسته شیمیایی اند مانند TiC/TiB2، TiC/TiNو TiN/TiB2 رشد هم جهت و تنظیم بافت در کنار متغیر های مهم فصل مشترک وجود دارند و خواص و عملکرد قطعه پوشش داده شده را تعیین می کنند. از طرفی ادغام مواد کووالانسی و یونی و مختل کردن رشد تک لایه ها ویژگی مهمی در پوشش هایی است که مواد آن ها از گروه های متفاوتی انتخاب شده باشند.
مواد دارای پیوند کووالانسی مانند AlN، BN، SiC و B4C را به سختی می توان به عنوان پوشش تک لایه استفاده کرد. چرا که چسبندگی مناسبی به زیرلایه فلزی ندارند. اما مشکلی در چسبندگی در فصل مشترک بین لایه های کووالانسی و کووالانسی یا کووالانسی و فلزی رسوب نشانی شده از فاز بخار وجود ندارد. بنابراین، مواد سخت کووالانسی می توانند در کامپوزیت های چند لایه قرار بگیرند و از این طریق به عنوان مواد ضد سایش روی زیرلایه اعمال شوند. این مواد به طور خاص، خواص کارکرد در دمای بالا را افزایش می دهند.
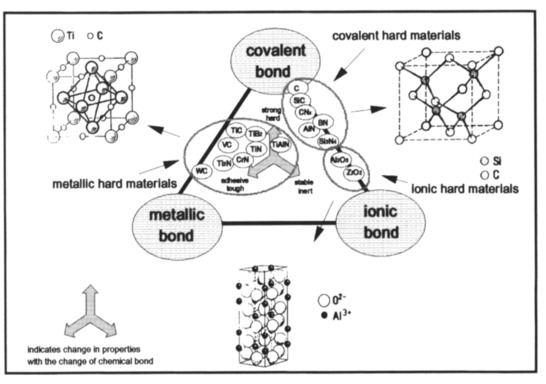
شکل ۵: دسته های مختلف مواد دارای ساختاری با مشخصات کریستالی
۶.پیشرفت های صورت گرفته در پوشش های چند لایه PVD
برای اثبات مناسب بودن طراحی چند لایه برای پوشش های PVD، چیدمان های مختلف زیادی مورد بررسی قرار گرفته اند.
- آماده سازی و بررسی های آزمایشی
پوشش های چند لایه جدید در دستگاه پاشش مگنترون Z ۵۵۰ آماده شدند. پوشش ها به طور غیر فعال بر روی زیرلایه سخت کاربید تنگستن، در محیط آرگون و فشار ۴.۰ پاسکال با توان ویژه ی W/cm2 3/11 رسوب نشانی شدند. قبل از رسوب نشانی زیرلایه ی پولیش آیینه ای شده در حمام مافوق صوت استون تمیز شده و در خلاء به کمک بمباران یون آرگون اچ پاششی شد. تمامی فیلم ها به ضخامت کلی ۵ میکرومتر رسوب نشانی شدند. فیلم های چند لایه با حرکت دادن زیرلایه به زیر مواد هدف مختلفی تولید شدند. ریز سختی (به روش ویکرز) تا دمای ۱۰۰۰ درجه سانتیگراد و همچنین چقرمگی به روش پالمکویست و هرتزین اندازه گیری شد. بررسی خواص تریبولوژی به کمک آزمایش سایش پین روی دیسک انجام شد. ضریب اصطکاک لغزشی و سایش لغزشی پوشش های تک لایه و چند لایه در مقابل فولاد، بدون هیچ لوبریکانتی اندازه گیری شدند.
- پوشش های حاوی مواد فلزی سخت
اطلاعات ریز سختی پوشش های چند لایه حاوی لایه های فلزی سخت در شکل 6 مشخص شده است. تک لایه های TiC و TiN به ترتیب مقادیر سختی ۲۷۰۰ و ۲۸۰۰ ویکرز را نشان دادند در حالی که پوشش های نیمه پایدار TiBC و TiBN مقادیر بسیار بیشتر ۴۸۰۰ و ۴۹۰۰ ویکرز را از خود نشان دادند. پوشش های 7 لایه TiN-TiBC-TiN مطابق با انتظار سختی بیشتری از پوشش های تک لایه TiN و TiC نشان دادند. با مقایسه کردن پوشش ۱۰۰ لایه TiN-TiC-TiBC با پوشش TiN-TiC که حاوی 50 لایه TiN و 50 لایه TiC هرکدام به ضخامت کلی ۵۰ نانومتر بوده است، مشخص می شود که افزودن لایه های ۲ نانومتری TiBC سختی را به مقدار قابل توجهی افزایش می دهد و تا حدود ۳۹۰۰ ویکرز بالا می برد.
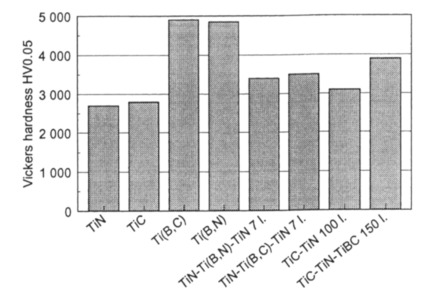
شکل ۶: ریزسختی فیلم های چند لایه و تک لایه فلزی
ضرایب اصطکاک پوشش ها در شکل ۷ مشخص شده اند. این ضرایب برای پوشش های تک لایه و ۷ لایه در محدوده ۰.۳۵ (TiC) و ۰.۹۵(TiBN) هستند. پوشش های متشکل از ۱۰۰ تک لایه TiC و TiN ضرایب اصطکاک پایین ۰.۲۳ را نشان می دهند. مشخصه این پوشش ها نرخ سایش پایین در آزمون پین روی دیسک و عمر لبه ی بالا در حین برش فولاد است که در شکل 8 مشخص شده است. پوشش های ۷ لایه در مقایسه با پوشش های تک لایه ی TiC و TiN عمر لبه ی بیشتری از خود نشان دادند در حالی که پوشش های نیمه پایدار TiBC و TiBN کمترین طول عمر ابزار را داشتند که مطمئنا این اتفاق به علت تجزیه شدن در دماهای بالا حین ماشین کاری است.

شکل ۷: ضرایب اصطکاک در مقابل فولاد و آلومینا برای پوشش های سخت فلزی اعمال شده به صورت تک لایه و چند لایه
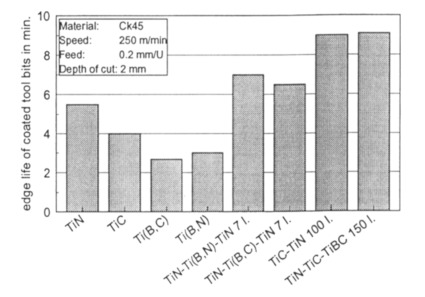
شکل ۸: عمره لبه ابزار برش پوشش داده شده با پوشش های سخت فلزی به صورت چند لایه و تک لایه (عمر لبه = اولین تغییر در شرایط برش)
- پوشش دهی با مواد سخت فلزی و کووالانسی
پوشش های چند لایه که دارای ۱۵۰ لایه ( ۱۰۰ لایه TiC/TiN و 50 لایه میانی متشکل از مواد سخت کووالانسی با ضخامت ۲ نانومتر) هستند، به طور کلی با مقادیر سختی بالاتر از ۳۰۰۰ ویکرز شناخته می شوند که در پوشش های 100 لایه TiC/TiN بدون مواد کووالانسی نیز سختی بالای این مقدار است (مطابق شکل ۹). اما تفاوتی که وجود دارد این است که پوشش های حاوی B4C سختی های بسیار بالاتری از خود نشان می دهند که این اتفاق به دلیل سختی شدید B4C است. لایه ی میانی B4C با ضخامت ۲ نانومتر سختی را بیش از ۱۰۰۰ ویکرز نسبت به پوشش چند لایه TiC/TiN بدون لایه میانی بالا می برد. تمامی پوشش های چند لایه ضرایب اصطکاک پایینی در مقابل فولاد 100Cr6 و Al2O3 نشان می دهند ( در محدوده ۰.۲۵ یا کمتر، مطابق با شکل ۱۰) و نرخ سایش کمی در آزمون پین روی دیسک دارند.
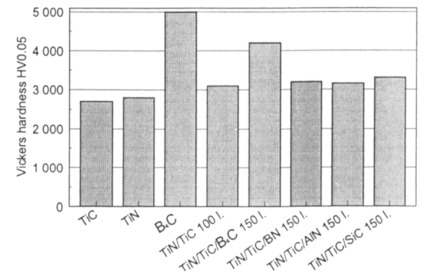
شکل ۹: مقادیر ریز سختی در پوشش های تک لایه و چند لایه مختلف
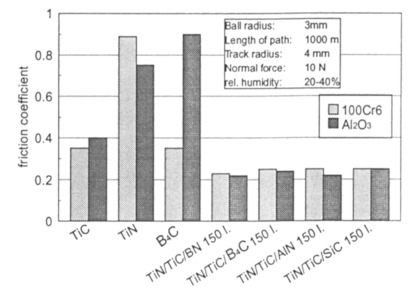
شکل ۱۰: ضریب اصطکاک در مقابل فولاد 100Cr6 و آلومینا برای پوشش های مختلف تک لایه و چند لایه
پوشش های چند لایه، علی الخصوص پوشش های حاوی لایه های B4C، AlN و BN عمر لبه ی بسیار خوبی از خود نشان می دهند که حتی از پوشش های چند لایه TiC/TiN بیشتر است (شکل ۱۱ و ۱۲ را ببینید) .
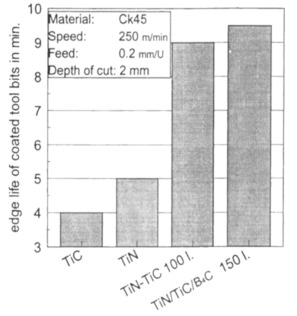
شکل ۱۱: عمر لبه ابزار پوشش دهی شده با پوشش های چند لایه و تک لایه (عمر لبه = اولین تغییر در شرایط برش)
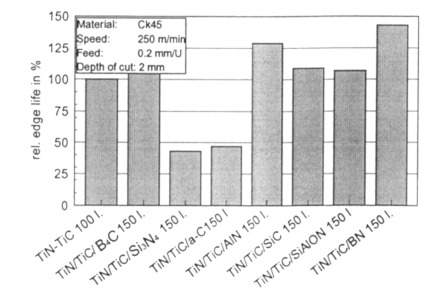
شکل ۱۲: عمر لبه نسبی در ابزار برش پوشش دهی شده به صورت چند لایه با لایه های میانی متشکل از مواد کووالانسی سخت. (عمر لبه ابزار پوشش دهی شده با پوشش 100 لایه TiC/TN صد درصد درنظر گرفته شده است)
پوشش های چند لایه حاوی لایه های آمورف کربن یا Si3N4 به علت چسبندگی کم به لایه های فلزی TiN و TiC کمترین عمر ابزار را دارند.
مقادیر نسبتا زیاد سختی در دمای بالا در پوشش های چند لایه حاوی لایه های AlN، BN و B4C (طبق شکل 1۳) خواص تریبولوژی مناسب و عملکرد عالی برش را در ابزار پوشش داده شده با پوشش های چندلایه حاوی مواد سخت فلزی و کووالانسی به همراه دارد.
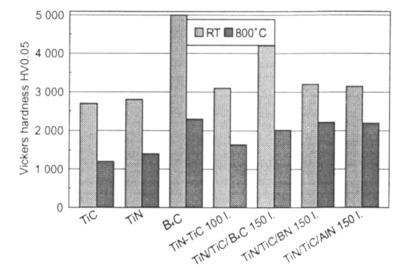
شکل ۱۳: ریزسختی مواد پوشش مختلف برای پوشش های تک لایه و چند لایه در دمای اتاق و دمای ۸۰۰ درجه سانتیگراد
- نتایج و بحث
ابزار پوشش داده شده با مواد TiC و TiN به صورت چندلایه، کاهش سایش بسیار بیشتری از ابزار پوشش دهی شده با همین مواد اما به صورت تک لایه نشان دادند. با معرفی لایه های میانی بسیار نازک (۲ الی ۱۰ نانومتر) متشکل از مواد کووالانسی سخت، مقدار کاهش سایش باز هم افزایش یافت. با توجه به طبیعت مواد کووالانسی، انحلال لایه ی نازک درون لایه های همجوار فلزی خود ( طبق شکل ۱۴ برای AlN، BN و Al2O3) و یا عدم انحلال و تفکیک لایه ی نازک ( طبق شکل ۱۵ برای B4C و SiC) قابل مشاهده است. توجیه کاهش سایش زیاد را می توان در سختی بالای پوشش های چند لایه در دماهای بالا پیدا کرد. این اتفاق به طور ویژه در پوشش های حاوی لایه های میانی B4C، BN و AlN قابل مشاهده است. پوشش های چند لایه چقرمگی هرتزین ۶۰ تا ۱۰۰ نیوتون را در مقابل چقرمگی پایین ۵۰ تا ۶۰ N برای پوشش های تک لایه TiC و TiN از خود نشان دادند.
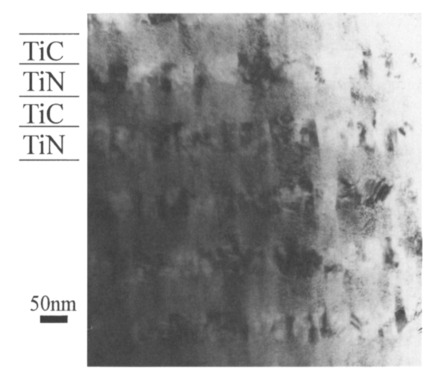
شکل ۱۴: تصویر TEM پوشش 100 لایه TiC/TiN حاوی لایه های میانی ۲ نانومتری Al2O3 به صورت محلول
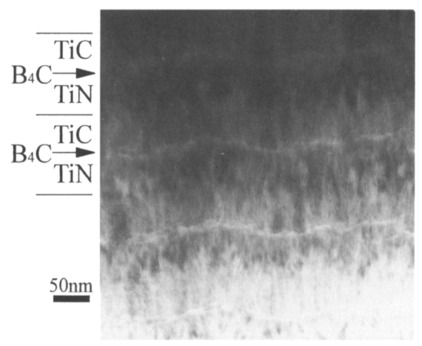
شکل ۱۵: تصویر TEM پوشش 100 لایه TiC/TiN حاوی لایه های میانی 2 نانومتری B4C به صورت تفکیک شده
- پوشش های شبه چند لایه
جالب توجه است که بسیاری از پوشش های تک لایه PVD در واقع می توانند پوشش های شبه چند لایه باشند. این اتفاق به دلیل تغییر زاویه ب برخورد ذرات به سطح زیر لایه و همچنین تغییر فاصله از کاتد به طور متناوب است که موجب تغییر در شدت رسوب نشانی و در نتیجه تغییر ترکیب، چگالی، بافت و تنش های ممکن می شود. در نتیجه، خواص و رفتار اجزای پوشش متکی بر حرکت زیرلایه به هنگام پوشش دهی خواهد بود. این اتفاق می تواند علت ناکارآمدی پوشش دهی انجام شده با یک فرآیند یکسان PVD اما شرایط متفاوت زیرآیند و چرخیدن آن باشد.
۸.مفاهیم فنی پوشش های چند لایه PVD در مقیاس صنعتی
تلاش های بسیاری در ابعاد جهانی برای انتقال مفاهیم پوشش های جدید به فرآیندهای تولید تجاری وجود دارد. برای پوشش دهی ابزار CVD و PVDفرآیندهای متداول هستند. به دلیل وجود محدودیت در امکان تغییر دهی اتمسفر گازی به طور دوره ای در طی فرآیند پوشش دهی، تکنیک های CVD با توجه به تعداد لایه های قابل دستیابی در پوشش های چند لایه محدود شده اند. رایج ترین فرآیندهای PVD برای رسوب نشانی پوشش های مقاوم در برابر سایش شامل آبکاری یونی و فرآیند های قوسی و پاششی است. پوشش چند لایه می تواند اجزای فلزی ، اجزای غیر فلزی یا هر دو را به طور همزمان در حین رشد فیلم تغییر دهد. برای جلوگیری از تغییر اجزای غیر فلزی در حالت پوشش دهی فعال، محدودیت های ذکر شده در بالا در مورد تغییر متناوب گاز اتمسفر، اینجا نیز وجود دارد. با در نظر گرفتن تمام خصوصیات فرآیندهای مختلف PVD ، فرایند پاششی مناسب ترین روش برای رسوب نشانی چند لایه است. تحقق فنی مفاهیم پیشرفته پوشش دهی در مقیاس صنعتی یک چالش بزرگ برای مهندسی سطح و به ویژه در فرآیند پاشش است.
۹.جمع بندی و چشم انداز
فیلم های نازک چند لایه کامپوزیتی مفهومی برای طراحی مواد کاربردی و ساختاری است. در این مواد عملکردهای شیمیایی ، فیزیکی ، مکانیکی و تریبولوژیکی می توانند برای کاربردهای خاص تنظیم شوند. همانطور که برای مواد بالک چند فازی سرامیکی ای شناخته شده است، می توان تنظیم ترکیب مواد و ریزساختار را برای بهینه سازی استحکام و مقاومت در پوشش های سخت به کار برد. سختی در دمای بالا، که مسبب عملکرد خوب در تنش های مکانیکی و حرارتی بالا است، توسط مفهوم چند لایه ای کردن پوشش قابل افزایش است.
پوشش های متشکل از چند تک لایه (با چند لایه اشتباه نشود( CVD و PVD (۳-۱۳ تک لایه) می توانند تا حدودی ساییدگی را در مقیاس صنعتی کاهش دهند. فرآیندهای PVD به خوبی برای رسوب نشانی پوشش های چند لایه در محدوده۱۰۰ تا ۱۰۰۰ لایه و در نتیجه بالا بودن کسر حجمی فصل مشترک، مناسب هستند و امکان تنظیم استحکام و چقرمگی در پوشش را دارند. انتخاب مناسب مواد و تنظیم تعداد و ضخامت تک لایه ها و همچنین تنش و کرنش پوشش باعث کاهش سایش فوق العاده بالا برای بسیاری از کاربردها می شود. حجم و ساختار فصل مشترک مستقیماً با خصوصیات و مقاومت در برابر سایش اجزای پوشش داده شده ارتباط دارد. مکانیسم های بهبود خواص و عملکرد توسط پوشش های چند لایه هنوز به خوبی درک نشده اند. مکانیسم های سخت سازی مختلف (ساختار ریز دانه، انحراف دهی به ترک ها ، کاهش تمرکز تنش ، نانو پلاستیسیته، تنش متناوب و میدان های کرنشی)، برهم کنش مواد مختلف ، تقویت تک لایه ها توسط لایه های مجاور و کاهش تنش های پسماند و ضریب اصطکاک ممکن است در تغییر خواص موثر باشند. فصول مشترک در پوشش های چند لایه PVD مکان هایی برای اتلاف انرژی هستند. خصوصیات این مکان ها (رشد، ترکیب و ساختار) به شدت به مواد دو طرفشان و همچنین پارامترهای ساخت پوشش بستگی دارد. شباهت مناطق فصل مشترک (به طور معمول ۱-۳ نانومتر برای پوشش های PVD) به ماده لایه ای که به عنوان بستر برایشان عمل می کند بیشتر است. مواد آمورف معمولا اجازه ی نفوذ بسیار زیادتری از سوی ذرات رسوب دهی شده به درون خود نسبت به مواد کریستالی می دهند. فناوری PVD امکان رسوب نشانی مواد نیمه پایدار را نیز فراهم می آورد. این مواد جدید را می توان با محصور کردن در یک چیدمان چند لایه به سوی کریستالی شدن با ساختار مد نظر، سوق داد.
در شرایط سایش شدید و پیچیده پوشش های چند لایه می توانند با طراحی و انتخاب مواد مناسب(از جمله مواد نیمه پایدار) ، تنظیم تعداد و ضخامت تک لایه ها، ساختار فصل مشترک و ساختار نانو یا نقوص شبکه تک لایه ها تبدیل به گزینه مناسبی برای پوشش دهی شوند .
تحقق فنی این تئوری امید بخش در مقیاس صنعتی یک چالش برای مهندس سطح و به ویژه برای تکنیک PVD است. رسوب نشانی پاششی (فعال یا غیر فعال) مطمئناً منعطف ترین فرآیند برای پوشش های چند لایه است. فرآیندهای ترکیبی (قوس/ پاششی یا یونی/ پاششی) از اهمیت ویژه ای در آینده برخوردار هستند.