درحال حاضر، رایج ترین پوشش تزئینی برای قطعات محتلف، پوشش های PVD سیاه رنگ هستند. به طور کلی رنگ سیاه به راحتی با فرآیند PVDحاصل می شود و می توان گفت که تمامی تامین کننده های پوشش PVD امکان تولید این نوع پوشش را دارند. اکثریت قریب به اتفاق روش های تولید پوشش سیاه رنگ درحال حاضر مبتنی بر سیستم DLC (کربن الماسی شکل) یا ترکیبات فعال پایه تیتانیومی (به عنوان مثال TiC،O) است. با این حال، پوشش های DLC دارای تنش های داخلی بالایی هستند که می تواند در چسبندگی آنها را به زیرلایه محدودیت ایجاد کند. از سوی دیگر، استفاده از گاز حاوی کربن مانند متان یا استیلن در این روش منجر به آلودگی نسبتاً قابل توجهی در محفظه پوشش دهی می شود و برای پمپاژ گاز کافی و مناسب و چسبندگی خوب لایه های پوشش به زیرلایه، نیاز به تمیزکاری مکرر وجود خواهد داشت.
از دیگر مشکلات موجود، مشکل دوپوششه کردن است. دوپوششه کردن در مواقعی که ایراداتی از جمله نقاط کوچک سفید رنگ که یکی از نقص های معمول پوشش های سیاه است ظاهر می شوند، ضروری است. در صورتی که چسبندگی لایه دوم به لایه ی اول به آسانی امکانپذیر باشد، صرفه جویی در زمان قابل توجهی در فرآیند دو پوششه کردن ایجاد خواهد شد. اما در روش پوشش دهی DLC، این اتفاق به دلیل چسبندگی ضعیف بسیار دشوار است.
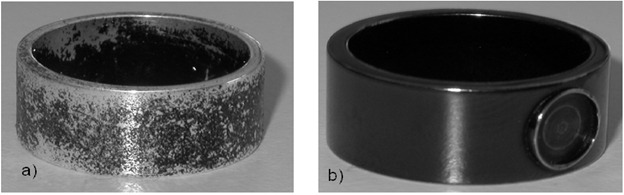
شکل ۱: مقایسه رفتار سایشی دو قطعه پوشش دهی شده به روش PVD DLC) a) و PVD Ti (N, C, پس از قرار گیری در معرض آزمون سایش به مدت 48 ساعت
در صورتی که پوشش دارای نقص های جدی تری (مشکلات چسبندگی به زیرلایه، وجود لکه های ناشی از خشک شدن و غیره) باشد، لازم است که لایه ی اول را به صورت شیمیایی، قبل از مرحله دوم پوشش دهی تضعیف و نازک نمود. در این مواقع، مقاومت بسیار خوب در برابر خوردگی لایه های پوشش به یک مشکل واقعی تبدیل می شود: انحلال شیمیایی پوشش به دلیل ریزساختار بسیار متراکم و آمورف، دشوار است و محلول شیمیایی نمی تواند از طریق تخلخل ها به درون پوشش نفوذ کند.
از طرف دیگر ، پوشش های Ti ,C, O)که به کمک CO2 به عنوان گاز واکنش دهنده ایجاد می شوند، مشکلات ذکر شده را نخواهند داشت. آلودگی کمتر، تنش های داخلی نسبتاً کم و امکان دو پوششه کردن مستقیم بدون نیاز به لایه برداری و انحلال شیمیایی پوشش در صورت بروز ایراد، باعث می شود که از این پوشش ها استقبال خوبی شود اما با این حال، یکی از اشکالات اصلی آنها سختی و مقاومت در برابر سایش (HV ≅ 400) نسبتا کم است. این نوع پوشش بیشتر برای قطعات داخلی ساعت (قطعات موتور ساعت، پل ها، صفحه ها، عقربه ها و …) توصیه می شود.
پوشش های TiC / TiCN، بسته به شرایط رسوب دهی می توانند طیفی از رنگ خاکستری روشن تا خاکستری تیره ایجاد کنند. با افزودن هیدروکربن های بیشتر، رنگ این پوششها از یک رنگ خاکستری بسیار تیره به سیاه تغییر می یابد.
از میان پوشش های دیگر مورد مطالعه برای تولید رنگ سیاه، پوشش های پایه TiAl به لطف مقاومت در برابر اکسیداسیون در دماهای بالا، محبوبیت بیشتری دارند. پوشش های TiAlN با توجه به تارگت ممکن است رنگی بسیار تیره با سایه هایی از آبی یا بنفش ایجاد کنند، که بدین ترتیب نمی توان از آنها برای ایجاد پوشش های سیاه خالص استفاده نمود. در صورتی که تارگت غنی از آلومینیوم باشد، (به عنوان مثال AlTi 70:30) امکان ایجاد رنگ سیاه بدون سایه بیشتر وجود دارد، اما در این حالت ، تنش های داخلی پوشش افزایش می یابد، که اثر سو بر چسبندگی دارد. تنشهای داخلی تا GPa 8 برای بایاس زیرلایه در محدوده -100 ولت تا -200 ولت گزارش شده است. به همین دلیل این نوع پوشش ریسک بالای پاشش داشته، و استفاده از آن به ویژه در پوشش دهی تزئینی قطعاتی با هندسه پیچیده، مانند بند یا قاب ساعت کاملاً نامناسب است. از سوی دیگر، یافتن مواد تارگت با کیفیت برای این ترکیب در بازار بسیار سخت بوده و این ترکیبات گران هستند.
تاکنون ترکیبات بسیاری از لایه های تیتانیوم و آلومینیوم از منظر تزئینی برای پوشش دهی مورد بررسی قرار گرفته اند که از این بین می توان به تارگت کامپوزیتی (50:50) و با رسوب نشانی همزمان از تیتانیوم و آلومینیوم خالص اشاره کرد. از مزایای رسوب نشانی همزمان، امکان تنظیم رنگ بسیار آسان با تغییر دادن ولتاژ اعمالی به هریک از کاتد ها در حین پوشش دهی است.
استفاده از نیتروژن به عنوان گاز واکنش دهنده ممکن است منجر به افزایش بیش از حد حداقل درخشندگی (L*=50) شود. این مقدار برای رنگ سیاه واقعی باید کمتر از 40 باشد (L*<40). از سوی دیگر در صورت تشکیل نیترید های TiAl، سایه های از رنگ آبی در رنگ سیاه ایجاد خواهد شد (b*<0). بهترین نتیجه بدست آمده با استفاده از TiAl(C,O) و گاز واکنش دهنده CO2 بوده است که در آن مقادیر L* در حدود 42 و a* و b*نزدیک به صفر (رنگ بدون سایه و خنثی) بوده اند.
در شکل 2، خلاصه ای از نتایج بدست آمده بر اثر استفاده از گاز های واکنش دهنده ی O2، CO2 و N2 را برای پوشش Ti(C, O) مشاهده می کنید.
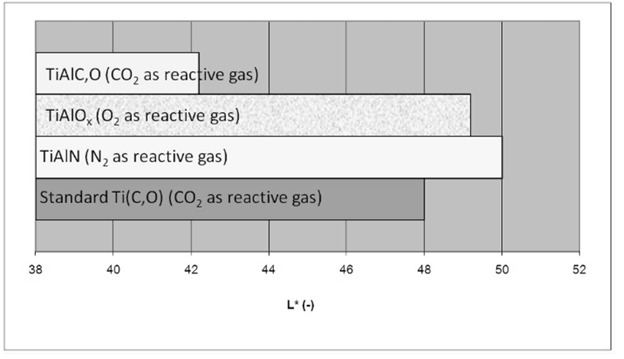
شکل ۲: مقادیر حداقل درخشش (L*) بدست آمده برای تارگت های تیتانیومی با استفاده از گازهای واکنش دهنده متفاوت
در حال حاضر، پوشش های TiAl (C, O, N) PVD تزئینی در مقایسه با پوشش های PVD DLC محبوبیت بالایی در میان ساعت سازان کسب کرده اند. این پوشش ها دارای مشخصه های زیر می باشند:
- رنگ سیاه شدید و بدون سایه ( a* و b* نزدیک به صفر)
- مقاومت به سایش بالاتر از پوشش های دیگر
- تنش های درونی کم
- امکان تنظیم و تکرار رنگ مناسب
- ایجاد آلودگی کمتر در محفظه پوشش دهی
- امکان پوشش دهی مجدد و دوپوششه کردن به طور مستقیم.