خلاصه
امروزه آلومینیوم در کنار فولاد پرکاربرد ترین ماده فلزی محسوب می شود. مشخصه های مکانیکی آلومینیوم باعث گستردگی زمینه های کاربردی آن، به خصوص در سازه هایی که به مواد سبک احتیاج دارند، شده است. به منظور بهبود مشخصه های آلومینیوم ار قبیل استحکام بالاتر و ماندگاری بهتر، آلیاژهای جدید آلومینیوم توسعه یافته اند و محققین همچنان در تلاشند تا بتوانند به طرق مختلف از نقات قوت آلومینیوم در کاربردهایی استفاده کنند که تا کنون از مواد دیگری که دارای سختی بالاتر و مفاومت به سایش هستند استفاده می شده است. برای اعمال پوشش های مقاوم به سایش روی سطح آلومینیوم چندین روش وجود دارد که روش نوین PVD به علت سازگاری با محیط زیست جایگزین خوبی نسبت به روش های مرسوم اعمال پوشش می باشد.
هدف این مقاله بررسی امکان پذیر بودن اعمال پوشش TiN روی آلیاژ آلومینیوم AlMgSi1 به روش PVD قوسی و بدون آسیب زدن به زیرلایه حساس به حرارت است. برای آماده سازی سطح آلومینیوم از فرآیند های ماشین کاری و تمیزکاری مختلفی استفاده شده است. رابطه پیش عملیات انجام شده روی سطح زیرآیند و مشخصه های پوشش بررسی شده و تاثیر متغیر هایی مانند اچ کردن، ولتاژ بایاس، زمان پوشش دهی و همینطور چیدمان قطعات در محفظه خلاء مورد آزمایش قرار گرفت. به منظور دستیابی به بهترین نرخ رسوب نشانی، ریزسختی و بار خراش بحرانی پوشش های طبقه بندی شده و چندلایه (TiN و Ti) روی سطح آلیاژ آلومینیوم نشانده شدند. برای مشخصه یابی رفتار مقاومت به سایش آلومینیوم از آزمایش سندبلاست خاصی استفاده شد. در نهایت روندی مناسب برای اعمال فیلم نازک محافظ روی آلومینیوم با هدف اقزایش مقاومت به سایش، به کار گرفته شد.
مقدمه
با رسوب نشانی پوشش های سخت به روش PVD بر روی زیرآیند آلومینیوم، مشکلات مختلفی به علت نقطه ذوب پایین زیرآیند و همچنین تشکیل لایه ی اکسید روی آن بوجود می آید. پیدا کردن راه حل برای این مشکلات متکی به دانش پایه ای در خصوص آلومینیوم است.
آلومینیوم خالص ( با درصد خلوص %۹۹.۹۹۹) ماده ای ناپیدار در کاربرد به عنوان سازه است چرا که استحکام تسلیم آن 20 نیوتون بر میلی متر مربع بوده و همچنین دمای تبلور مجدد آن -۶۰ تا ۴۰- درجه سانتی گراد است که استحکام بخشی با کار سرد را ناممکن می سازد. افزودن عناصر جانبی مانند Fe ، Si و Ti به مقدار %۰.۰۱ دمای تبلور مجدد را تا بیش از ۲۰۰درجه سانتی گراد بالا می برد. کاهش دادن خلوص آلومینیوم همچنین باعث می شود که در حالت آنیل نرم شده، استحکام کششی تسلیم و سختی به ترتیب به مقادیر Rpo.۲ = ۲۵ N mm-۲ و Rm=۷۰ N mm-۲ افزایش یابند (در خلوص %۵.۹۹) درحالیکه افزایش طول در نقطه شکست به مقدار A۱۰=۵۰% کاهش می یابد. علت افزایش مقدار چقرمگی ساختار ریزدانه شده است، که به طور خاص به علت مقادیر کم تیتانیوم و بور ایجاد می شود. انحلال این عناصر در شبکه بلوری چقرمگی را افزایش می دهد. مس، آهن و سیلیکون موجب افزایش استحکام می شوند. افزایش بیشتر استحکام می تواند با انجام کار سرد حاصل شود.
افزایش مقاومت به خوردگی آلومینیوم می تواند در خلوص های بالا بهتر بدست بیاید. با در معرض هوای محیط قرار گرفتن آلومینیوم، لایه ای نازک و فشرده از اکسید در اثر برهم کنش فلز و اکسیژن و رطوبت هوا تشکیل می شود که محافظت از خوردگی را انجام می دهد. در صورتی که این لایه به طور مکانیکی یا شیمیایی آسیب ببیند یا برداشته شود، لایه ی جدیدی از اکسید آلومینیوم بلافاصله تشکیل می شود (اثر خود ترمیم شوندگی). لایه ی اکسید عمدتا شامل Al2O3 آمورف است. تشکیل اکسید عناصر آلیاژی دیگر از جمله منیزیم در لایه ی محافظ ممکن است بتواند خواص حفاظتی لایه را به طور محدودی بهبود بخشد. برخلاف لایه ی اکسیدی بسیاری از فلزات دیگر، لایه ی اکسیدی فشرده آلومینیوم چسبندگی به سطح خوبی از خود نشان داده و بنابراین حفاظت مناسبی در برابر اکسید شدن بیشتر فلز زیرلایه خود انجام می دهد. این خاصیت دلیل مقاومت بالای آلومینیوم در برابر اثرات جوی و بسیاری از مواد آلی و معدنی است.
لایه اکسیدی تشکیل شده بر روی آلومینیوم پولیش شده در اتمسفر بدون رطوبت در عرض چند دقیقه به ضخامت ۰.۰۰۱ میکرومتر می رسد. پس از گذشت چند روز، این لایه با سرعت رشد کاهش یافته ای به حدود دو تا سه برابر این ضخامت خواهد رسید. دماهای بالاتر (به طور مثال: عملیات حرارتی) سرعت رشد این لایه ی اکسیدی خنثی را افزایش می دهند. در اتمسفر مرطوب در لایه اکسیدی هیدروکسید نیز تشکیل شده و ضخامت لایه میتواند به بیش از ۰.۱ میکرومتر نیز برسد.
برای پوشش های PVD این رفتار اکسیدی آلومینیوم می تواند مشکل ساز باشد. بررسی نمونه های مختلف آلومینیوم که در زمان های متفاوتی تحت شرایط متنوع اتمسفری قرار گرفتند نشان داده است که انجام پولیش آینه ای قبل از انجام رسوب نشانی، آماده سازی مناسبی برای فرآیند پوشش دهی PVD قوسی خواهد بود. پس از انجام فرآیند اچ، لایه های اکسید موجود اثر منفی بر چسبندگی پوشش نخواهند داشت. در صورتی که نمونه ها برای مدت زمانی طولانی تحت اتمسفر گرم و مرطوب مانده باشند، لب پر شدن پوشش مورد انتظار است.
آلومینیوم آلیاژهای کارسخت پذیری را با بسیاری از عناصر آلیاژی تشکیل می دهد. مقادیر چقرمگی این آلیاژها می تواند از طریق عملیات حرارتی اصلاح شده ای مانند رسوب سختی، بهبود یابد. این عملیات حرارتی شامل سه مرحله زیر می باشد:
۱.عملیات حرارتی محلول سازی: از طریق آنیل در دماهای بالا ( کمتر از پایین ترین دمای ذوب فازهای موجود در آلیاژ) مقدار زیادی از عناصر آلیاژی در آلومینیوم محلول جامد تشکیل می دهند که باعث ایجاد اثرات رسوب سختی می شود.
۲.خنک کردن سریع (کوئنچ): از طریق کوئنچ کردن (به طور مثال در آب) محلول جامد اشباع شده از عناصر آلیاژی به شرایط فوق اشباع می رسد.
۳.پیرسختی: از طریق پیرسختی (در دمای اتاق یا دماهای متوسط) رسوبات از محلول جامد فوق اشباع جدا شده و منجر به افزایش استحکام کششی، استحکام تسلیم و سختی خواهند شد. این رسوبات که از طریق پیر شدن طبیعی آلیاژ در محیط ایجاد شده اند به طور منسجم و همدوس ایجاد می شوند. اما اگر به کمک دماهای متوسط پیر سازی انجام شود، فازهای نیمه پایدار ایجاد شده که با محلول جامد نیمه همدوس هستند. با روش پیرسازی مصنوعی (دماهای ۱۰۰-۲۰۰ درجه سانتیگراد)، خواص استحکامی سریع تر افزایش یافته و استحکام حداکثری بیشتر خواهد بود. پیرسازی در دماهای بیش از حد بالا و همچنین زمان های طولانی منجر به تشکیل فازهای ناهمدوس و بنابراین کاهش استحکام خواهد شد (فرا پیر شدن).
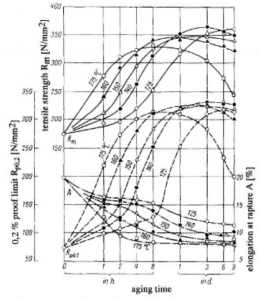
شکل ۱: خواص متفاوت آلیاژ AlMgSi1 با توجه به دما و زمان پیرسازی (دمای آنیل: °C 520 ، کوئنچ در آب)
آلیاژ AlMgSi1 به کار رفته در این پژوهش در بسیاری از زمینه ها کاربرد دارد( قوطی و جعبه، لوله، ورق، اجزای هواپیما، لوازم تزئینی اتوموبیل، سازه های کامیون ها، بدنه قایق، بدنه ماشین آلات، سازه های جوشکاری و محفظه های مواد غذایی). این آلیاژ به هر دو صورت طبیعی و مصنوعی قابل پیرسازی است، و اثر سخت شدن بر اثر رسوبات Mg2Si ایجاد میشود. بیشترین مقادیر استحکام از طریق پیرسازی مصنوعی بدست آمده و بنابراین اولویت پیرسازی آلیاژ با این روش است. اثرات عملیات حرارتی محلول سازی در دمای ۵۴۰-۵۲۰ درجه سلسیوس در شکل ۱ مشخص شده است. مقادیر سختی بر حسب زمان پیرسازی نیز در شکل ۲ آورده شده است. اندازه گیری سختی برینل، HB، کاربردی نبوده و بنابراین سختی ویکرز HV با توجه به استاندارد DIN 50 133 اندازه گیری شده است. در خصوص آلیاژ آلومینیوم، مقادیر سختی ویکرز حدود ۱۵ درصد بالاتر از برینل هستند.
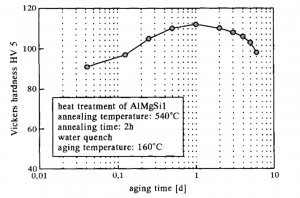
شکل ۲: سختی AlMgSi برحسب زمان پیرسختی
بهبود خواص سایشی آلومینیوم از طریق پوشش دهی TiN تنها زمانی ممکن است که سختی ماده ی زیرآیند مناسب باشد. درصورتی که زیرآیند بیش از حد نرم باشد، همانند شکل 3، این امکان وجود دارد که پوشش سخت TiN در زیر بار به روی زیرآیند پرس شده و لب پر شدن پوشش به دلیل تغییر فرم پلاستیک زیاد رخ بدهد. در خصوص آلیاژ های آلومینیوم دارای قابلیت عملیات حرارتی، اساساَ دو راهکار برای دستیابی به حداکثر سختی زیرآیند حین انجام پوشش دهی PVD وجود دارد. اول اینکه، آلیاژی انتخاب شود که دمای عملیات حرارتی آن مشابه دمای فرآِیند پوشش دهی باشد. این اتفاق اجازه خواهد داد که فرآیند محلول سازی و کوئنچ خود به خود حین فرآیند PVD القا شوند. راهکار دوم، که در این پژوهش از آن استفاده شده است، این است که با پایین نگه داشتن دماهای عملیات پوشش دهی تا حد ممکن، از تاثیر گذاری روی خواص استحکامی زیرآیند جلوگیری شود. این اتفاق علی الخصوص باید در مورد آلیاژهایی که به طور مصنوعی پیرسخت شده اند رعایت شود و دمای پوشش دهی PVD در مقادیری بسیار پایین تر از دمای پیرسازی نگه داشته شود. فناوری PVD دراین خصوص امکاناتی را پیشنهاد می دهد که در این مقاله بررسی می شوند.
لایه های اکسیدی که بر اثر تمایل ذاتی آلومینیوم به اکسیژن ایجاد می شوند، می توانند اثرات منفی بر استحکام پیوندهای پوشش و زیرلایه داشته باشند، به این دلیل که آنها مرزی خنثی و فشرده ایجاد می کنند و فرآیند نفوذ و یا هرنوع برهمکنشی بین پوشش و زیرآیند را مختل می کنند. در مقابل، تجربه هایی از پوشش دهی آلومینیوم، تیتانیوم و کروم بر روی فولادی که به طور موضعی اکسید شده باشد، نشان داده است که تشکیل اکسیدهای مخلوط چسبندگی پوشش را بهبود می بخشد. پَن[1] در پژوهش خود اشاره به لایه های اکسید درونی، متشکل از فازهای بین فلزی FeTiO3 و TiO2 کرده است که باعث بهبود چسبندگی پوشش TiC روی فولاد شده اند. پوشش های TiCدرصورتی که جزئی ترکیبی متشکل از مواد پوشش، لایه اکسیدی و مواد زیرآیند بر روی آلومینیوم ایجاد شود، چسبندگی بسیار مناسبی به زیرآیند آلومینیومی خواهند داشت. افزودن نیتروژن نیز می تواند این چسبندگی را بهبود ببخشد.
روش پژوهش
نمونه های استوانه ای AlMgSi1 به قطر ۲۰ میلیمتر و ارتفاع ۵ میلیمتر به مظور پوشش دهی انتخاب شدند. این نمونه ها به طور مصنوعی در شرایط دمایی۵۴۰درجه سانتیگراد به مدت ۲ ساعت محلول سازی شده، در آب کوئنچ شده و در دمای ۱۶۰ درجه سانتیگراد برای ۲۴ساعت پیرسخت شدند. به منظور پرداخت سطحی، از یک دستگاه لپینگ(براده برداری با سنگ ساینده و دوغاب) استفاده شد و قبل از عملیات پوشش دهی نمونه ها با کاغذ پولیش و امولسیون الماس ۶ میکرومتری پولیش شدند و سپس به روش مافوق صوت با تتراکلراتیلن و ایزوپروپان تمیز شدند. علیرغم تمیزکاری مافوق صوت، برخی از دانه های الماس در سطح آلومینیوم گیر کردند، بنابراین در آینده پیشنهاد می شود از ساینده های بسیار نرم برای عملیات پرداخت سطحی استفاده شود.
نمونه های آلومینیومی، به کمک دستگاه Interatom PVD ۲۰ به روش PVD قوسی پوشش دهی شدند. این نوع پوشش دهی به طور موفقیت آمیزی در ابعاد صنعتی برای پوشش دهی وسایل مختلف، به خصوص ابزارآلات استفاده می شود. برای پوشش دهی آلومینیوم، متغیرهای پوشش دهی باید آزموده شده و تنظیم گردند. در این پژوهش، علاوه بر متغیرهای استاندارد شامل بایاس، فشار گازهای ری اکتیو و توان تبخیرکننده، متغیر هایی از جمله تمیزی زیرآیند، میزان فعال بودن سطح، فاصله قوس از سطح، چیدمان نمونه ها در محفظه خلاء و ساختار پوشش مورد بررسی قرار گرفتند.
برای مشخصه یابی مقاومت به سایش نمونه های آلومینیوم پوشش داده شده، از آزمون سند بلاست استفاده شد. متغیرهای این آزمون طوری انتخاب شدند که بتوانند تمایز واضحی بین آلومینیوم بدون پوشش و پوشش دار ایجاد کنند. مواد بلاست (کوراندوم قهوه ای و سفید، ساچمه شیشه ای) در ابعاد مختلفی آزموده شدند. آزمون های سایش در نهایت با ساچمه های شیشه ای با اندازه ذرات ۹۲-۱۰۱میکرومتر، فشار پاشش ۱ اتمسفر، نازل تزریقی به قطر ۶ میلیمتر و فاصله پاشش ۵۰ میلیمتر انجام شدند. زاویه پاشش با هدف شبیه سازی کردن سایش حداکثری، به مقدار ۲۰درجه در نظر گرفته شد. زاویه های باز تر منجر به ایجاد حالتی می شوند که مقدار سایش کاهش یافته و مقادیر تغییر فرم پلاستیک بر اثر ضربه افزایش می یابد.
نتایج و بحث
عملیات حرارتی پیش از پوشش دهی اهمیت بسیار زیادی در پوشش دهی آلومینیوم به روش PVD دارد. در مدت زمان کوتاهی، لایه ای فشرده از اکسید آلومینیوم بر روی سطح تشکیل شده و رشد می کند. برای اینکه این لایه در کمترین ضخامت بماند تا بتوان به چسبندگی مناسبی بین پوشش و زیرلایه رسید، نمونه های آلومینیومی باید قبل از پوشش دهی تا حد آیینه ای پولیش داده شوند. معمولا اچ یون فلزی نیز قبل از انجام فرآیند PVD قوسی وجود دارد که در آن زیرآیند تحت بمباران یون های فلزی با انرژی بالا قرار می گیرد. اچ یون فلزی به طور کلی چسبندگی پوشش را بهبود می بخشد. انرژی یون های فلزی منتشر شده توسط تبخیر کننده قوسی از طریق بایاس زیرآیند محاسبه می شود. اگر بایاس زیرآیند بیش از حد بالا باشد، انرژی ذرات زیاد تر از حد لازم است و دما به سرعت افزایش می یابد. اگر بایاس خیلی کم باشد، پوشش تیتانیومی نرمی رسوب دهی خواهد شد. برای نمونه های آلومینیومی، اچ کردن کوتاه اما شدید بهینه ترین نوع است. در این حالت به محض افزایش بیش از حد دما فرآیند متوقف می گردد. لایه ی میانی تیتانیومی بهبودی در خواص پوشش دهی ایجاد نکرد.
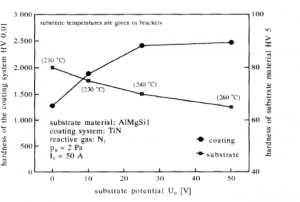
شکل ۳: سختی زیرآیند آلومینیومی و پوششTiN تبخیر شده با قوس برحسب تغییرات پتانسیل زیرآیند
در شکل ۳ مقادیر سختی زیرآیند و مواد پوشش نمونه های پوشش دهی شده آلومینیوم بر حسب ولتاژ بایاس نشان داده شده است. با افزایش ولتاژ بایاس سختی پوشش به مقادیر مناسب نظری نزدیک می شود، با این وجود مقادیر سختی زیرآیند به شدت کاهش می یابند. این کاهش سختی به علت فشار افزایش دمای بیش از حد است.