The term Physical vapor deposition was mentioned for the first time in 1966 in the book Vapor deposition, but before that in 1838, Mr. Michael Faraday used this method to deposit certain coatings. PVD method or physical vapor deposition is a new and emerging method in Iran’s industry, which basically includes several different methods without chemical reaction. In this method, layer growth is formed by evaporation or sputtering along with excited atoms, molecules or ions produced in the plasma. The purpose of this process is to create nanometer-thick thin layers composed of primary metals, alloys, nitrides, oxides, carbides, borides, sulfides, silicates, fluorides, or a combination of them. Physical coating from the vapor phase includes the following steps:
1- Converting the volatile substance into a gaseous state through evaporation, sublimation or cathodic sputtering
2- The transfer of atoms (molecules) from the evaporation source to the substrate under vacuum pressure
3- The formation of bonds between atoms and the coating surface
In general, the main mechanisms of the physical coating process from the vapor phase are the separation of atoms from the surface by means of radiation, electron beam, heat, electric or ion arc (For example, the argon ion hits the surface and causes atoms to be thrown from the target material to the substrate, resulting in the formation of a layer).
Plasma is obtained by ionizing gas atoms and molecules. The plasma state can be created by heating the gas in such a way that the temperature of the gas can be raised to several hundred thousand degrees. Plasma plays a key role in transporting ions and forming a coating on the surface of the desired part.
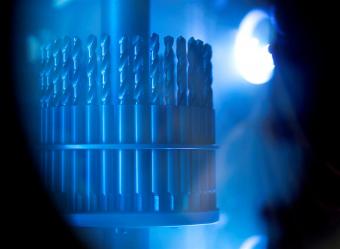
Figure 1- The formation of plasma space in the vacuum chamber
Advantages of PVD coating:
1- Excellent adhesion at low coating temperatures
2- Covering parts with complex shapes
3- Coverage uniformity
4- Increasing the reliability and useful life of the part cover
5- Replacement of expensive materials
Disadvantages of PVD coating:
1- Connecting the sample to the electrode with high voltage
2- The need to work in a high gas pressure
3- The difficulty of local coverage
4- Lack of coating of internal surfaces
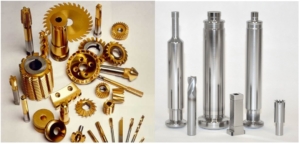
Figure 2: Gold (TiN) and silver (CrN) coating on industrial machining tools
Some of the characteristics of the PVD coating include resistance to erosion and scratches, creating a surface with very desirable features that increase the life of the parts, and a wide range of colors and shades.
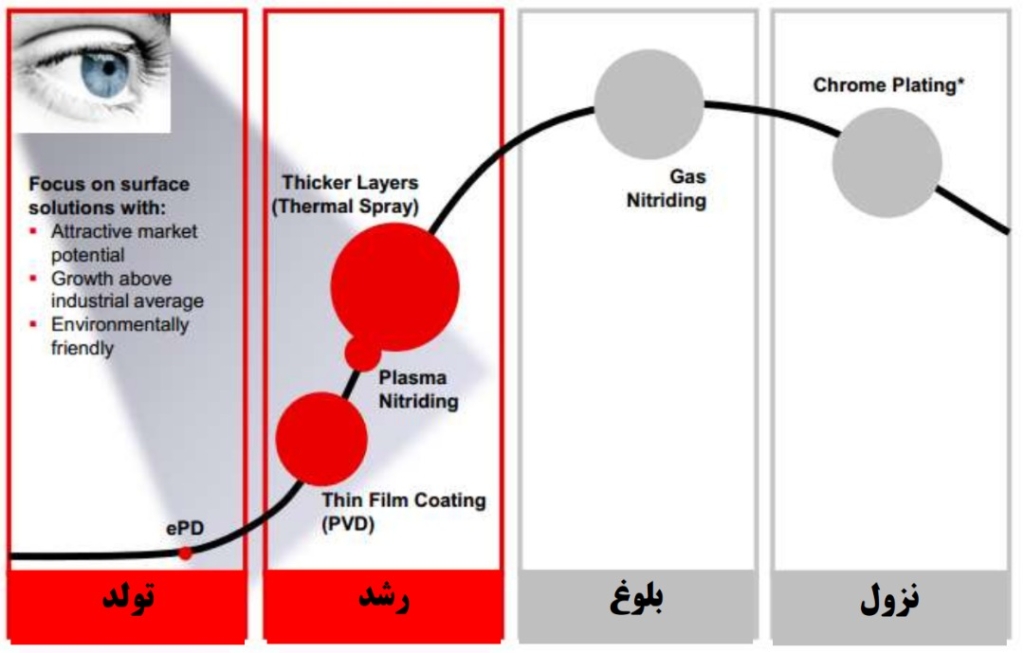
Figure 3- Performance comparison of different coating methods in the industry
Thin PVD coating layers are frequently used today to improve the efficiency of forming tools, cutting tools and mechanical elements. In all these applications, the surface hardness of the coated part is of particular importance because friction affects this part. By using coating methods, it is possible to restore many worn parts and reduce the production costs of parts.
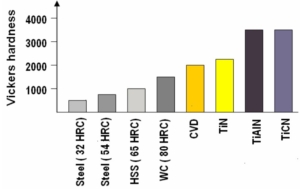
Figure 4- Comparison of surface hardness of materials with and without coating
Source: Nano engineering of hard and resistant coatings; Dr. Hassan Alamkhah