PVD coatings are produced on industrial and decorative parts in various colors with different structures for various applications.
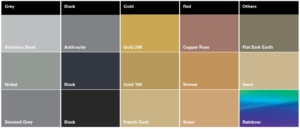
Figure 1 – Standard colors produced using PVD
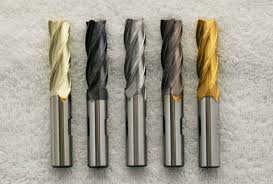
شکل۲- تولید مته های با پوشش PVD
First generation: The first coating created by the PVD method was hard nitride coatings of intermediate elements such as TiN, CrN and ZrN. The high hardness of these coatings was significant compared to high-speed steel and cemented carbide. Also, due to their attractive appearance, they were also considered for the decorative industry. The thermal stability of these coatings is not suitable for high speed machining applications. So that the TiN coatings are oxidized and decomposed at 450 degrees Celsius and will be destroyed.
Second generation: The thermal stability of single-phase coatings, including TiN, is obtained by adding alloying elements, including Cr, Al, and Y, into the TiN structure. For example, TiAlN nanostructure coatings, which are proposed as TiN substitutes and oxidation-resistant coatings. Despite its high hardness, due to the formation of a solid solution, it exhibits very good oxidation resistance. In this coating, by forming a nanometer thin layer of Al2O3 at high temperature, it will protect the coating against further oxidation.
The third generation: improvement of mechanical properties is achieved by creating multilayer and superlattice coatings. The term “superlattice” refers to multi-layered coatings with alternating layers with a thickness of less than 10 nm. One of the first examples of hypergrid coatings is TiN/VN and TiN/NbN coating. By choosing the right combination for multilayer coatings, it is possible to improve the properties of coatings such as resistance to wear, corrosion and oxidation and increase malleability.
Fourth generation: Nanocomposite coatings contain at least two phases: a nanocrystalline phase and an amorphous phase or two nanocrystalline phases such as TiAlSiNs. The combination of hard nanocrystalline grains (such as carbides and nitrides) and amorphous materials (such as DLC) with high elastic modulus has resulted in achieving high hardness and good elastic recovery. Nanocomposite coatings are usually known as ultra-hard coatings whose hardness value is more than 40 GPa.
Fifth generation: Recent efforts have focused on the development of hard, wear-resistant and low-friction coatings. For this purpose, materials such as graphite, MoS2 and oxide materials can be used in the nanocomposite coating. Wear-resistant and self-lubricating coatings have been developed using lubricating phases such as graphite, amorphous carbon and MoS2 inside the coating. The friction coefficient of self-lubricating coatings in this case will be between 0.1 and 0.01. Research shows that the wear properties of classic coatings are improved by using a thin layer of DLC (diamond-like) as the outer layer.
Industrial Parts |
coating | |||||
TiN | TiC | CrN | AlTiN | ZrN | DLC | |
micro hardness (HV) | 2000-2500 | 2700-3000 | 2100-2500 | 3000-3700 | 2200-2600 | 1500 |
Friction coefficient in dry state (µ) | 0.5 | 0.4 | 0.5 | 0.4 | 0.5 | 0.1 |
Coating thickness (µm) | 1-4 | 1-4 | 1-4 | 1-4 | 1-4 | 1-4 |
Oxidation temperature (֯C° ) | 500 | 400 | 650 | 900 | 550 | 400 |
Appearance color | Gold | Gray | silver | Dark purple-rose gold | bright golden | graphite grey |
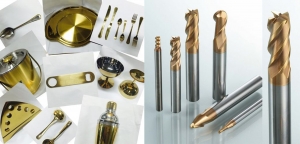
Figure 3- TiN coating created on tools and decorative parts
TiN Coating: Titanium Nitride is the most economical coating layer that has always been in demand by customers due to its attractive golden color. This coating was first produced by PVD method. This coating is used for a wide range of applications that require increased hardness, heat resistance, oxidation resistance and lubrication. It is also environmentally friendly and is used in the pharmaceutical and medical industries. It is also widely used in tool making industries to increase the life and wear resistance of cutting, drilling, etc. tools. In the decorative field, it is also widely used to cover faucets, ornaments, crystals, steel spoons and forks, ceramics, etc.
Source: Nano engineering of hard and resistant coatings; Dr. Hassan Alamkhah