Coating using physical vapor deposition (PVD) is divided into two general methods:
1- Evaporation
2- Sputtering
each of which is done with several different models that will be explained below.
1-1- Thermal Evaporation:
The evaporation process using tungsten filament is used to melt metals such as aluminum and copper that have a melting point of less than 1500 degrees Celsius. After the chamber pressure reaches 10-5 torr, a high current (about 100 to 200 amperes) is applied to the tungsten crucible through the copper electrode (with hydrogel) and causes the evaporation of the target material that is placed inside the crucible.
Advantages:
1- Inexpensive equipment compared to sputtering
2- Inexpensive target materials
3- Relatively high coating speed
4- low chamber temperature during the process (possibility of coating on plastic parts)
Disadvantages:
1- Low coverage density due to the low energy of vaporized materials (0.1-0.5 electron volts)
2- Weak adhesion of coating materials to the substrate
3- Impossibility of coating refractory metal materials
4- The possibility of presence of minor impurity of crucibles inside the coating
Despite the weak adhesion of this method, the use of this coating is appropriate and practical in cases where the coated part is not available and exposed to wear. For example, coating the interior wall of the car light bowl with aluminum allows for more light reflection.
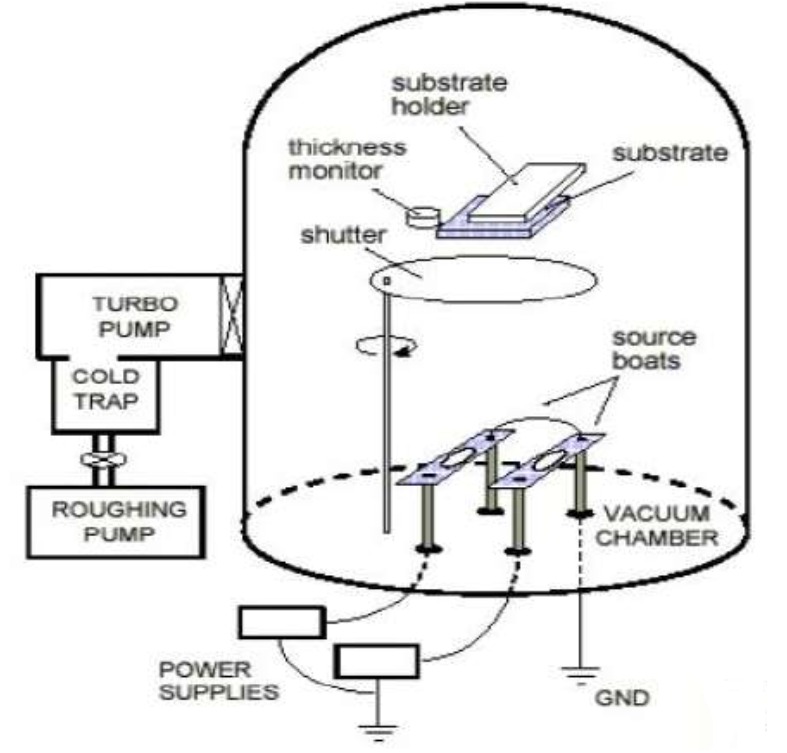
Figure 1- Thermal Evaporation method
2-1- Electron Beam Evaporation:
Due to the impossibility of coating refractory materials and ceramic materials with the Thermal Evaporation method, the evaporation method using an electron beam has been suggested. In this method, after applying a high current to the tungsten filament and heating it, the produced electron is focused by an electric field and is irradiated by traveling an angle of 270 degrees on the surface of the target material which is placed in a special crucible. Due to the very high energy of the electron beam, it will be possible to vaporize refractory materials and ceramic materials, including semiconductor and dielectric materials. The electron beam only melts and evaporates a small area of the substrate and causes the formation of a high purity layer on the substrate.
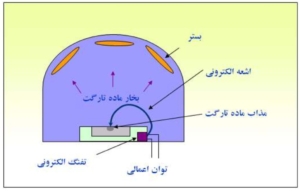
Figure 2- Electron Beam Evaporation method
Advantages:
1- Possibility of evaporation of all refractory and ceramic materials
2- Higher purity than the thermal evaporation method
3- No need for the presence of neutral gas during coating (pressure in the range of 10-5 to 10-6 Torr)
4- Relatively high coating speed
Disadvantages:
1- Due to the difference in the melting point and evaporation of materials, it is impossible to achieve accurate stoichiometry in composite and alloy materials.
2- More expensive equipment than Thermal Evaporation
Due to the possibility of coating materials with a high melting point, this method has been considered in the electronics, optics and semiconductor industries. Also, due to its high coating speed and the type of coating mechanism (columnar growth), in the last decade, TBC thermal barrier coatings have been commercialized for covering turbine blades in the aviation industry and are used by reputable companies around the world.
3-1- Cathodic Arc Evaporation:
In the Arc PVD process, electrical discharge occurs between two electrodes (anode and cathode) in a vacuum environment. A medium current is required to ionize and vaporize one of the electrodes. In this method, evaporation may take place on the cathode or on the anode. Cathodic arc PVD method is among the methods that are currently being used commercially in the Iranian industry. In this method, the formation of an electric arc is similar to the welding system, after the high current is established, the surface of the target (cathode) is ionized and the ionized atoms move towards the part. In the presence of reactive gas such as N2 in the atmosphere of the chamber, it will cause the formation of TiN metal nitride compound on the piece.
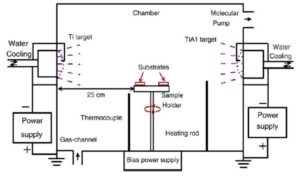
Figure 3- Schematic of the evaporation process using the cathodic arc method
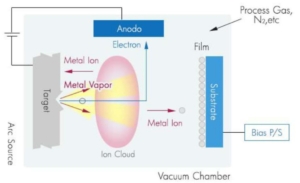
Figure 4- Plasma formation and coating in the cathode arc evaporation method
Advantages:
1- The possibility of coating all metals and forming metal nitrides and carbides
2- Due to the high energy of vaporization atoms, proper adhesion and density of the coating to the substrate
3- Relatively high coating speed
Using this method, it is possible to coat molds, tools and industrial parts on a commercial scale. Also, one of the other uses of this method is to create decorative coatings with various colors.
Disadvantages:
1- Due to the nature of the process, the presence of macro particles causes defects in the coating
2- Slight change in the stoichiometric composition of alloy materials
3- Non-use of non-conducting and semi-conducting targets in this method
2- Sputtering:
The sputtering process consists of removing the atom from the surface of the target material by sputtering gas (such as argon gas) and placing it on the substrate. In sputtering, plasma plays a significant role in removing atoms from the surface. The different steps that are formed in this method are as follows:
1- Argon gas atoms will be ionized due to the existence of a high potential difference between the cathode and the anode.
2- The positive argon ions strongly hit the negative potential where the target substance is located.
3- Argon ions bombard the target material, which will cause the material to be torn off and thrown towards the substrate. The sputtering benefit of metals is different from each other, for example, a metal like silver is more and faster than titanium (the sputtering benefit is the ratio of sputtered atoms and hit ions).
4- As a result, the desired thin layer is formed on the substrate.
5- Also, secondary and free electrons in the chamber collide with argon atoms and produce more ions, which will cause more plasma production for the sputtering process.
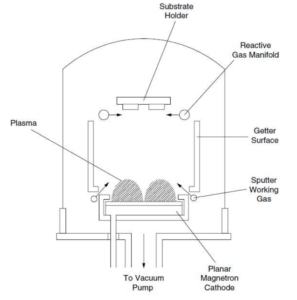
Figure 5- General schematic of Sputtering method
According to the type of applied potential and additional reactive gases, there will be different types of sputtering process. Types of sputtering process methods are:
1- DC Sputtering
2- AC Sputtering or RF
3- Reactive Sputtering
4- Magnetron Sputtering
5- HiPIMS (High power impulse magnetron sputtering)
Sources: nano engineering of hard and resistant coatings; Dr. Hassan Alamkhah